3D printing materials transform architectural and interior design concepts into tangible models, with selection directly impacting accuracy, durability, and visual appeal of client presentations. This guide analyzes three key material categories: versatile FDM filaments for rapid prototyping, high-detail resins for intricate elements, and durable powder-based options for functional models.
We examine critical mechanical properties, chemical resistances, and surface qualities essential for architectural applications, while outlining five decisive selection factors including equipment compatibility and cost considerations. By understanding these material characteristics, designers can effectively balance aesthetic requirements with structural functionality to create compelling physical representations that enhance client communication and project development.
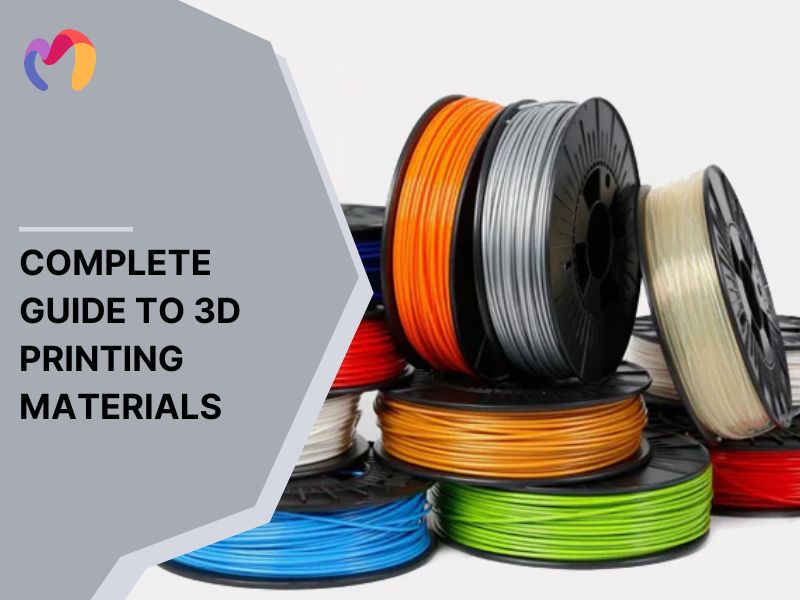
1. Fundamentals of 3D Printing Materials
3D printing uses various materials, including standard thermoplastics like PLA, ABS, and PETG, high-performance options like Nylon and TPU, and composite filaments infused with carbon fiber or wood. Each material has unique properties that affect print strength, precision, and durability.
PLA (Polylactic Acid) melts at low temperatures, adheres well, and is beginner-friendly but lacks heat resistance. ABS (Acrylonitrile Butadiene Styrene) withstands impacts but needs a heated enclosure to prevent warping. PETG (Polyethylene Terephthalate Glycol) balances durability and flexibility while resisting moisture, making it useful for functional parts.
For demanding applications, Nylon offers strength but absorbs moisture and needs high extrusion temperatures. TPU (Thermoplastic Polyurethane) provides elasticity for flexible parts. Composite filaments, reinforced with carbon fiber or wood, enhance strength and aesthetics but require fine-tuned settings. Choosing the right material ensures prints meet functional and structural requirements while minimizing common printing issues.
2. 3 Essential Types of 3D Printing Materials
In 3D printing, material selection determines the properties and applications of the final product. The market is dominated by three primary categories. FDM filaments like PLA and ABS are easy to use and versatile. Resin materials in SLA and DLP offer high detail and smooth finishes. SLS powders create strong, self-supporting parts for industrial use. Choosing the right material ensures precision, durability, and performance in 3D-printed products.
2.1. FDM Filament Materials
Fused Deposition Modeling (FDM) relies on diverse filament materials, each serving specific needs in 3D printing. Common options include PLA (Polylactic Acid), ABS (Acrylonitrile Butadiene Styrene), PETG (Polyethylene Terephthalate Glycol-Modified), and nylon. Each has distinct properties influencing strength, flexibility, and printability.
PLA is the most widely used due to its ease of printing, biodegradability, and precision. It suits prototypes and general-purpose prints but lacks high heat resistance. ABS offers greater toughness and heat tolerance, making it suitable for functional parts. It can be post-processed with acetone for a smooth finish but requires an enclosed printer to reduce warping.
PETG balances ease of use and durability. It resists moisture and impact better than PLA while remaining easier to print than ABS. Nylon is ideal for high-performance parts. It combines strength, flexibility, and wear resistance, making it useful for mechanical components and end-use products.
Specialty filaments, such as carbon fiber-reinforced and metal-infused PLA, provide added rigidity, heat resistance, or conductivity. However, their abrasive nature requires hardened nozzles. These materials are used for applications where standard filaments fall short.
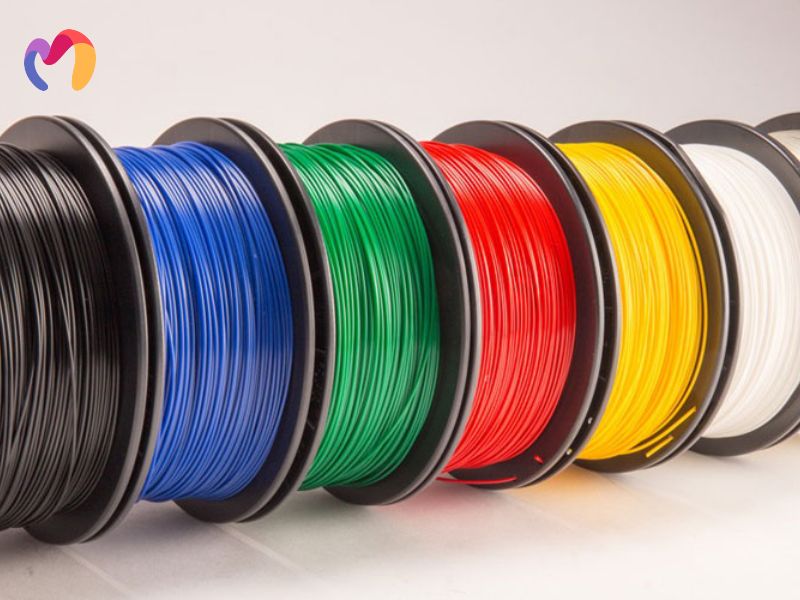
2.2. Resin-Based Materials (SLA/DLP)
Resin-based 3D printing, used in SLA (Stereolithography) and DLP (Digital Light Processing), delivers high-resolution details and smooth surfaces. These technologies rely on photopolymer resins, liquid materials that solidify under ultraviolet (UV) light through photochemical reactions.
Photopolymer resins contain photoinitiators that trigger polymer cross-linking when exposed to UV light. This curing process ensures strong, precise, and isotropic parts, making these resins essential in dentistry, jewelry making, and precision engineering.
Different resin formulations serve specific needs. Standard resins produce detailed prototypes. Tough resins handle mechanical stress, making them ideal for functional parts. Clear resins allow light transmission, useful for optical applications. Castable resins enable lost-wax casting for metal fabrication.
Handling these materials requires caution. Uncured resins pose health risks, making protective gear and safety protocols necessary. By following proper procedures, users can maximize resin-based printing for intricate, high-performance components.


2.3. Powder-Based Materials (SLS)
Selective Laser Sintering (SLS) 3D printing fuses polymer powders, mainly nylon (PA), into strong, functional parts. A laser selectively sinters powder layer by layer, enabling complex geometries without support structures.
SLS printing uses various nylon formulations. PA12 suits general applications, while glass-filled nylon increases stiffness and strength for demanding parts. Material selection depends on mechanical needs and environmental conditions.
Process control is crucial. Maintaining chamber temperature prevents warping, while recycling unused powder ensures efficiency. Mixing refreshed and virgin powder in precise ratios maintains part quality.
Industries like aerospace, automotive, and consumer goods rely on SLS for prototypes, functional components, and small-batch production. The powder bed naturally supports prints, allowing intricate designs that traditional manufacturing cannot achieve.
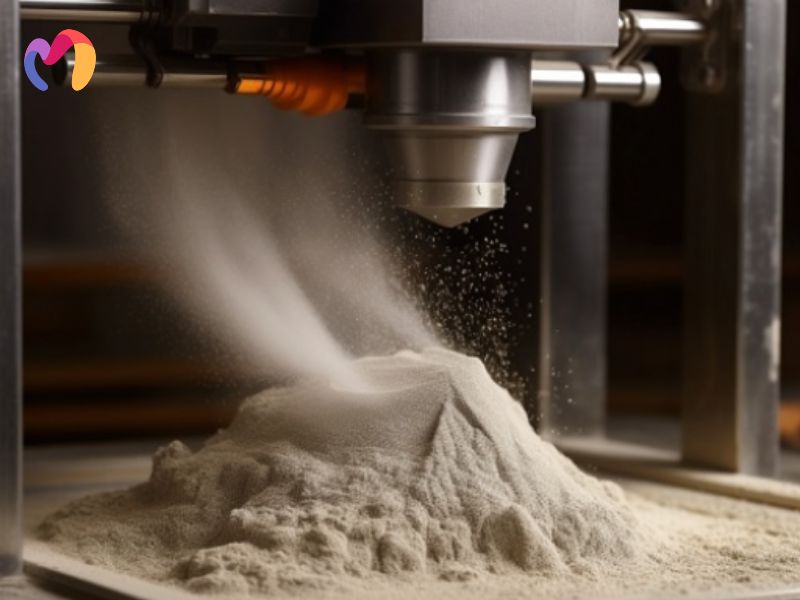
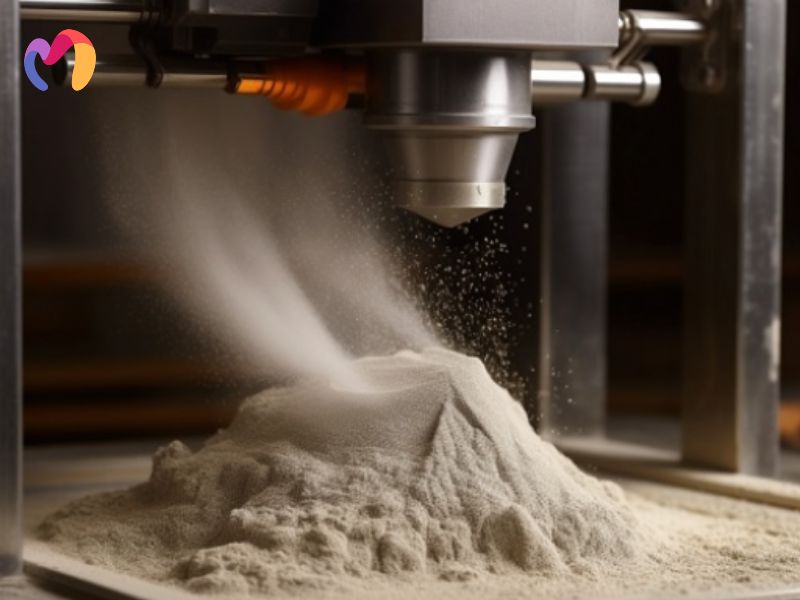
3. 3 Important Properties of 3D Printing Materials
Choosing the right 3D printing material requires evaluating mechanical behavior, chemical resistance, and surface quality. These properties determine a material’s suitability for prototypes, functional parts, and end-use products.
- Mechanical Characteristics
Strength, flexibility, and temperature resistance define a material’s performance under stress. ABS resists impact, making it durable for functional parts. PLA holds tensile strength but can be brittle. TPU stretches without breaking, while polycarbonate (PC) stays rigid under pressure.
Heat tolerance is critical for components exposed to high temperatures. PC and PEEK maintain stability under heat, while PLA softens quickly, limiting its use in warm environments. Wear resistance also matters—nylon excels in friction-heavy applications, ensuring durability.
- Chemical and Environmental Properties
Chemical stability affects a material’s longevity and safety. PLA withstands alcohols but degrades in acids. ABS and PETG resist chemicals, suiting industrial applications. Nylon repels oils and solvents, making it ideal for mechanical parts.
Environmental exposure also impacts material lifespan. ABS weakens under UV light, while PETG holds up outdoors. PLA degrades over time, making it eco-friendly but unsuitable for extended use in harsh conditions. Safety is another concern—ABS emits fumes during printing, requiring ventilation, while PLA remains a safer choice.
- Surface Quality and Aesthetics
Surface texture and finish impact both function and appearance. FDM prints show layer lines, while SLA and SLS produce smoother results. Post-processing enhances aesthetics—ABS responds well to acetone smoothing, while PLA requires sanding.
Material selection also affects the final look. Wood-filled PLA mimics natural grains, while metal-infused filaments can be polished to a metallic sheen. Post-processing techniques refine surfaces, ensuring a professional finish.
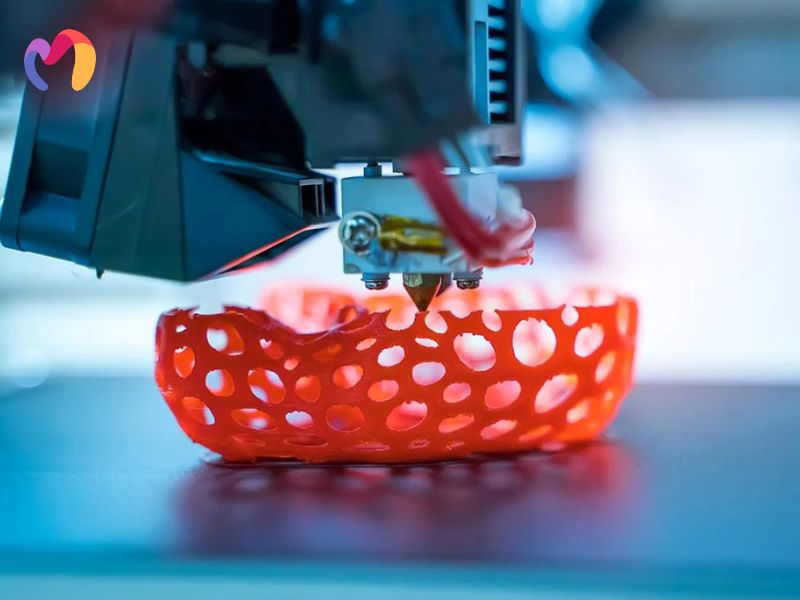
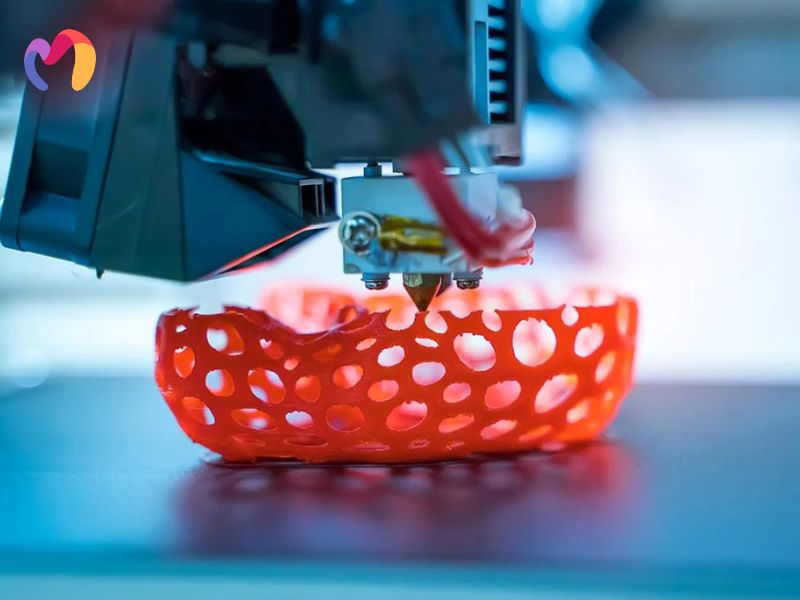
4. 5 Critical Factors Affecting Material Selection
Selecting the right 3D printing material is key to achieving optimal performance and durability. Several factors shape this decision, each influencing the final outcome.
- Environmental Conditions Matter: The operating environment dictates material choice. High-temperature applications require heat-resistant options like ABS or Polycarbonate. In humid settings, moisture-resistant materials such as PETG prevent degradation.
- Printer Compatibility Is Non-Negotiable: Not all printers support every material. Check nozzle temperature, build plate specs, and whether the printer can process specialty filaments before committing to a material.
- Cost Impacts Feasibility: Budget constraints influence selection. PLA offers a cost-effective solution for prototyping, while advanced materials like Nylon or PVA bring higher durability at a steeper price.
- Application-Specific Properties Drive Selection: Tensile strength, flexibility, and chemical resistance must align with the part’s intended use. Each material has unique mechanical traits that impact functionality.
- End-Use Determines Durability: The material must withstand real-world conditions. Choosing wisely ensures the part functions as intended, lasts longer, and performs reliably in its intended role.
5. Conclusion
The article delves into the diverse arena of 3D printing materials, highlighting three primary categories: thermoplastics, metal composites, and advanced materials. It details their properties and selection criteria, emphasizing that the right material choice is crucial for successful printing, whether for functional prototypes or final parts.
By leveraging this knowledge, individuals can enhance their 3D printing endeavors. For more insights, read related blog posts or discover suitable 3D models at 3DMAXTER.
3DMAXTER LTD
- Email: [email protected]
- Phone: +1 (929) 450-2898
- Address: 95-38 Queens Blvd, Rego Park, NY 11374, USA
Thank you for choosing 3DMAXTER LTD.