Types of 3D Modeling refers to the process of creating three-dimensional objects in a digital environment using specialized software. When searching for information about 3D modeling types, users typically face two main challenges: difficulty understanding the complex technical aspects of each method, and uncertainty in selecting the most suitable approach for their specific projects.
This comprehensive guide addresses these challenges by analyzing the 11 most common types of 3D modeling, from Wireframe Modeling to Image-Based Modeling. Each method is clearly explained with its advantages, limitations, and practical applications, enabling readers to make informed decisions for their projects.
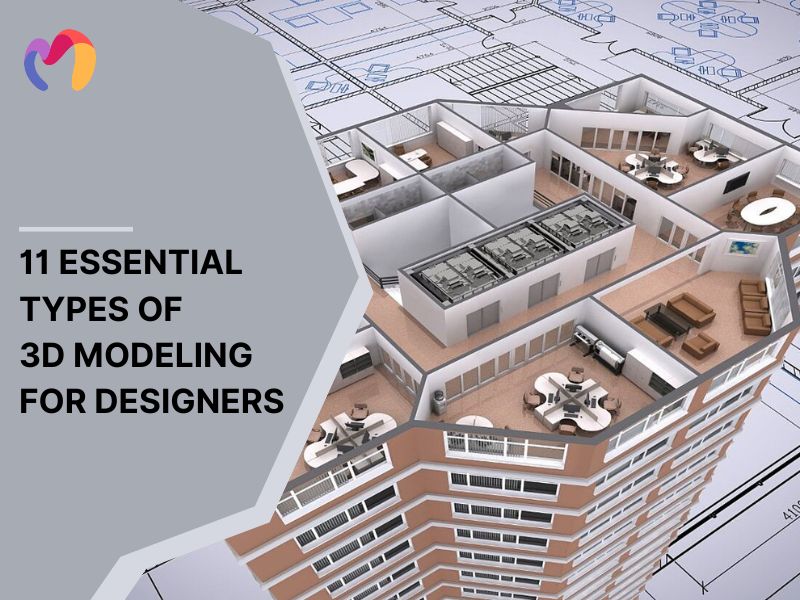
1. Top 11 Core Types of 3D Modeling
3D modeling encompasses 11 core techniques, each tailored to specific project needs. Each method offers unique strengths, from rapid prototyping to intricate surface detailing, enabling creators to tackle complex design challenges with confidence.
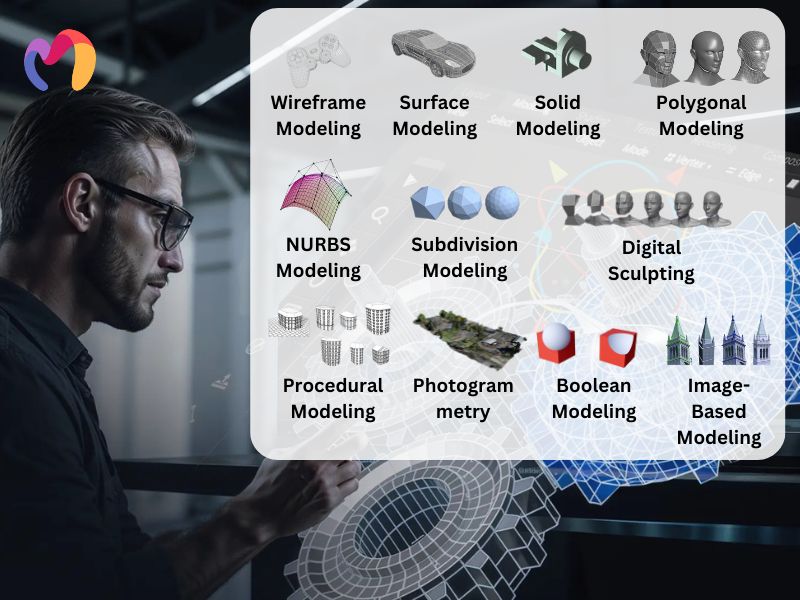
1.1. Wireframe Modeling
Wireframe modeling creates digital skeletons of 3D objects through connected lines and vertices. It generates transparent frameworks that reveal object structure and spatial relationships.
- Advantages: Wireframes allow rapid creation and iteration of designs. They require minimal system resources and provide a fast way to visualize design concepts.
- Limitations: Wireframes lack detail and realism compared to fully developed 3D models. They do not effectively convey texture, color, or surface features.
- Common Use Cases:
- Building design and planning: Architects use wireframes to map out spatial relationships in structures.
- Product prototyping: Designers quickly prototype products to visualize and refine concepts.
- Video game pre-production: Developers use wireframes to plan level layouts and character movements.
- Manufacturing layouts: Engineers validate design functionality before physical production.
- Scientific modeling: Researchers create wireframe models for simulation and analysis.
- Vehicle design: Automotive designers sketch wireframes to explore form and structure.
1.2. Surface Modeling
Surface modeling transforms wireframe designs into complete 3D objects by adding curved surfaces and faces. It emphasizes aesthetics and precise outer surfaces, building smooth, visually accurate shapes.
- Advantages: Surface modeling creates smooth, visually accurate designs, making it ideal for products where appearance and external features are the primary concern. It offers high precision in defining curves and complex surfaces.
- Limitations: While surface models excel at shaping outer surfaces, they do not include internal properties like volume or mass. This makes them unsuitable for detailed engineering analysis or simulations involving internal structure.
- Common Use Cases:
- Automotive Design: Creates vehicle bodies and aerodynamic components
- Aerospace Engineering: Develops aircraft fuselages and wing structures
- Product Development: Shapes consumer goods and packaging
- Industrial Design: Forms machinery and equipment shells
- Architectural Design: Builds complex building facades and structures
1.3. Solid Modeling
Solid modeling creates complete 3D objects with precise mathematical definitions and physical attributes. It includes both outer shells and internal properties, enabling detailed engineering analysis and manufacturing validation.
- Advantages: Solid modeling provides full dimensional control, internal data, and material properties. It is perfect for detailed engineering and analysis, supporting simulations such as stress testing and material flow.
- Limitations: Solid models can be computationally intensive, especially when designing complex objects. They require significant processing power, making them less efficient for rapid prototyping or visual exploration.
- Common Use Cases:
- Engineering Design: Engineers use solid modeling for creating mechanical components with precise measurements and physical properties.
- Product Prototyping and Manufacturing: Solid models are used to create digital twins for testing and validation before physical production.
- Architectural Design: Architects use solid modeling for creating detailed building structures and testing design functionality.
1.4. Polygonal Modeling
Among the best types of 3D modeling, polygonal modeling builds 3D objects using geometric faces (polygons), typically triangles or quadrilaterals, connected into a mesh. It is widely favored for its efficiency and flexibility in animation and gaming.
- Advantages: Polygonal modeling allows for fast rendering and efficient use of memory. It provides flexibility and direct control over the mesh, making it ideal for real-time applications like games and interactive media.
- Limitations: While polygonal modeling is efficient, it struggles with smooth curves and accurate surface details. Highly complex models can be resource-intensive, and achieving realistic organic forms requires additional processing or techniques like subdivision.
- Common Use Cases:
- Video Games: Used extensively for creating 3D characters, environments, and objects in real-time gaming.
- Animation and Visual Effects: Ideal for modeling characters and objects in films and TV shows, especially when real-time performance is necessary.
- Virtual Reality (VR): Polygonal models are used in VR for creating interactive environments that need to render quickly.
>> See more: What Is A Polygon in 3D Modeling? Compare High-Poly Vs Low-Poly Ones
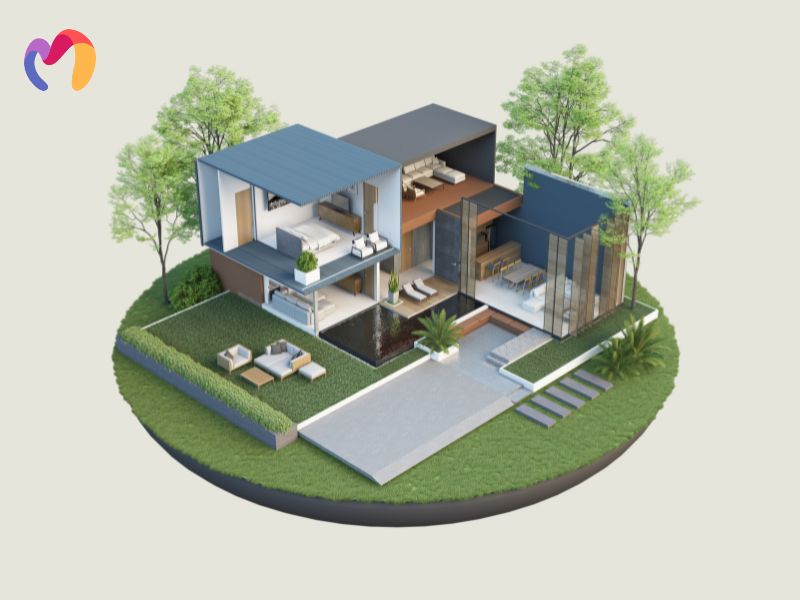
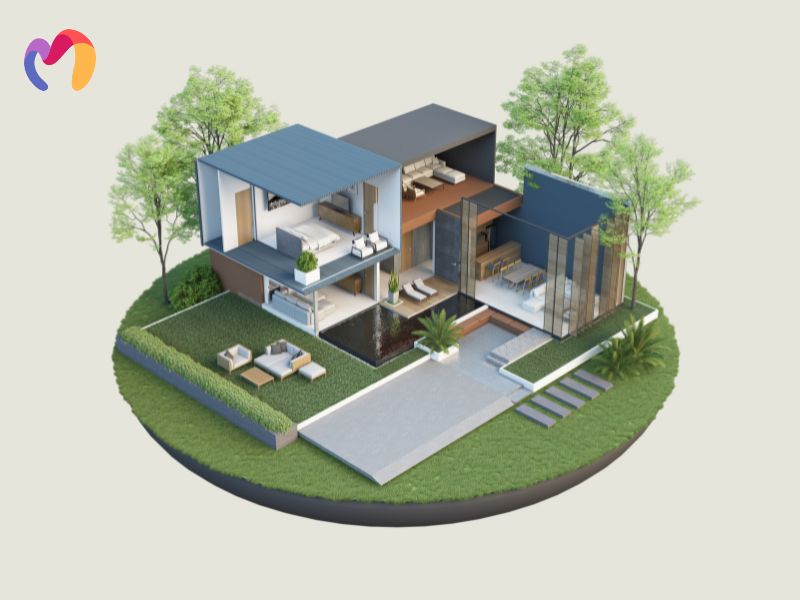
1.5. NURBS Modeling
NURBS (Non-Uniform Rational B-Splines) modeling uses control points to create smooth, flowing curves and surfaces with mathematical precision. It is ideal for designing organic and highly accurate shapes.
- Advantages: NURBS offers pinpoint accuracy and smooth curves, ideal for creating organic shapes or highly detailed surfaces. It provides excellent control over surface continuity and allows for precise model creation.
- Limitations: NURBS can be difficult to manipulate, particularly for beginners. Additionally, creating complex shapes can be computationally demanding and requires advanced software knowledge.
- Common Use Cases:
- Automotive Design: NURBS is commonly used to model vehicle bodies, focusing on aerodynamic precision and surface quality.
- Aerospace Engineering: Helps in creating smooth, precise components such as aircraft fuselages and wings.
- Product Engineering: Ideal for modeling consumer products where smooth, high-quality surfaces are needed.
- Industrial Design: Used for creating parts and tools that require exact surface specifications.
1.6. Subdivision Modeling
Subdivision modeling starts with simple polygon shapes and smooths them into complex surfaces through strategic subdivisions. It bridges the strengths of polygonal and NURBS modeling.
- Advantages: Subdivision modeling allows for the quick creation of both low-poly and high-poly models, making it ideal for organic shapes. It provides a balance between ease of use and the ability to produce highly detailed models.
- Limitations: Requires careful mesh control to avoid geometry issues.Poor mesh topology can lead to problems like surface distortions or uneven smoothing, requiring manual correction.
- Common Use Cases:
- Character Modeling: Widely used for creating detailed, smooth surfaces in characters, especially human faces or creatures.
- High-End Visualization: Used in film and video games for creating realistic, detailed characters and objects that require smooth surfaces.
- Product Design: Helps create smooth, detailed designs for consumer products, especially those with organic shapes.
1.7. Digital Sculpting
Digital sculpting mimics traditional clay sculpting in a virtual environment, allowing artists to shape models directly using digital tools. Programs like ZBrush and Mudbox offer powerful sculpting capabilities, ideal for highly detailed models.
- Advantages: Digital sculpting is ideal for creating intricate, lifelike details in organic models, such as characters and creatures. It allows for a more intuitive, hands-on approach to modeling compared to traditional techniques.
- Limitations: The high computational demand can be taxing, especially for complex, high-resolution models. Additionally, digital sculpting has a steep learning curve, making it challenging for beginners to master.
- Common Use Cases:
- Character Creation: Digital sculpting is used for creating highly detailed and lifelike characters, particularly for animation and video games.
- Creature Design: Artists use digital sculpting to design complex, organic body structures for use in games, films, or concept art.
- High-Detail Environments: Sculpting tools are used for creating highly detailed, organic environments, such as landscapes, rocks, and other natural features.
1.8. Procedural Modeling
Procedural modeling uses algorithms to generate complex 3D environments, such as cities or landscapes, through a set of predefined rules. This method is often used when large-scale structures need to be created quickly and consistently.
- Advantages: Procedural modeling allows for rapid creation of expansive environments with a high degree of consistency. It is particularly useful in generating large-scale, detailed landscapes or urban settings where manual modeling would be inefficient.
- Limitations: The main limitation is that it offers limited control over fine details. Since the 3D modeling process is based on algorithms, small adjustments to the design can be difficult to implement without disrupting the overall model.
- Common Use Cases:
- Urban Planning: Used to simulate large cityscapes, helping urban planners visualize complex infrastructures.
- Environmental Design: Generates large natural environments, like forests or mountains, for games and simulations.
- Architecture: Automates the creation of large-scale structures or complex building facades in architectural projects.
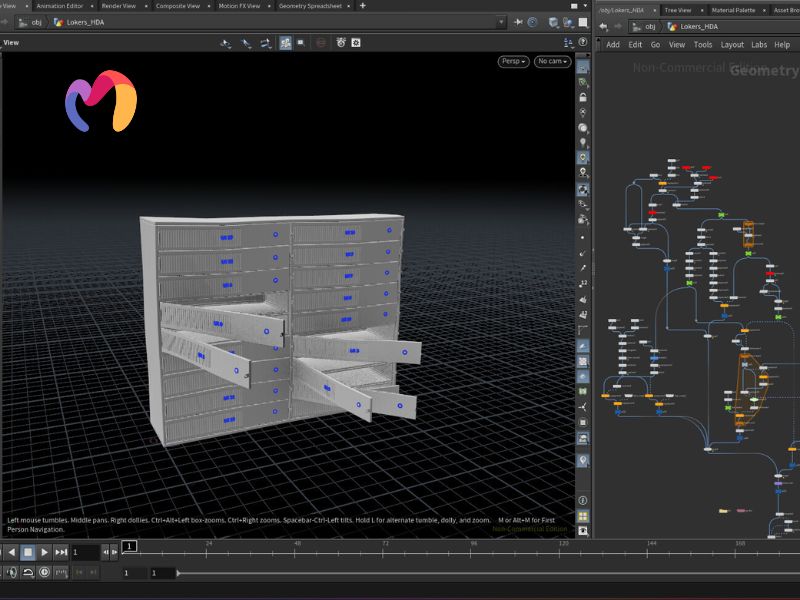
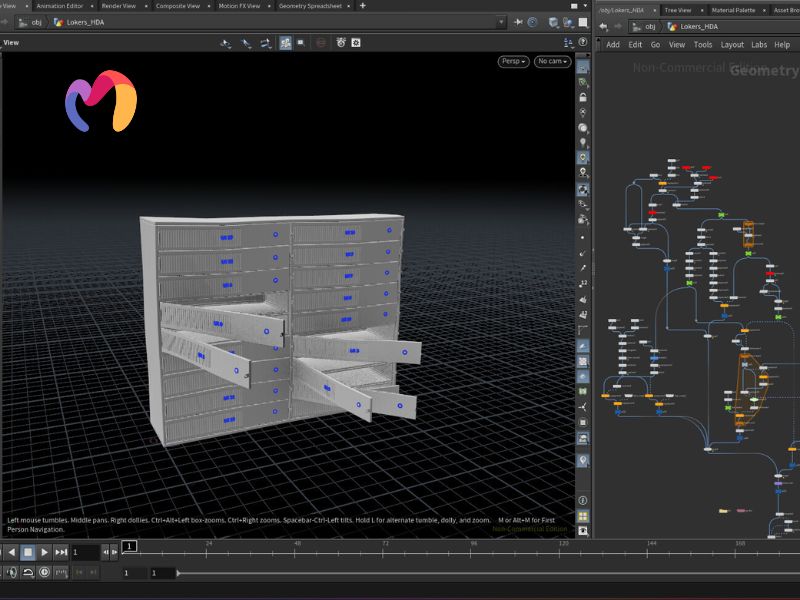
1.9. Photogrammetry
Photogrammetry is the process of converting multiple photographs into a 3D model by analyzing spatial data and textures from different viewpoints. This is one of the great types of 3D modeling that is ideal for creating realistic models based on real-world objects.
- Advantages: Photogrammetry offers highly accurate measurements and true-to-life textures, making it an excellent choice for creating realistic 3D models. It also allows for the rapid digitization of real-world objects.
- Limitations: The quality of the resulting model is heavily dependent on the quality of the input photographs. Additionally, it requires complete coverage of the subject to ensure accurate results.
- Common Use Cases:
- Archaeology: Used to digitally preserve artifacts and historical sites for research or virtual display.
- Film and Entertainment: Creates realistic environments and props for movies, TV shows, and video games.
- Virtual Reality: Used to generate immersive, real-world environments for VR applications.
- Architecture: Helps document and analyze buildings for restoration or renovation projects.
1.10. Boolean Modeling
Boolean modeling uses operations such as union, subtraction, and intersection to create complex 3D shapes from simple geometric objects. This method is commonly used to design objects with clear, defined geometry.
- Advantages: Boolean modeling allows for rapid creation of complex shapes and provides clean, precise results. It is especially useful for tasks that require frequent iteration or adjustment of geometric forms.
- Limitations: Boolean modeling can struggle with highly organic or freeform shapes. Additionally, improper use of Boolean operations can lead to non-manifold geometry or other issues that require further correction.
- Common Use Cases:
- Architecture and Engineering: Used to design and refine geometric elements in buildings or infrastructure projects.
- Product Development: Facilitates rapid prototyping by combining and refining simple shapes into complex designs.
- Mechanical Design: Engineers use Boolean modeling to create and adjust detailed parts and assemblies.
1.11. Image-Based Modeling
Image-based modeling converts photographs into 3D models by extracting shape data from multiple images. This technique is efficient for creating accurate, lifelike models without the need for physical scanning.
- Advantages: Image-based modeling quickly produces accurate 3D representations of real-world objects. It is cost-effective and ideal for projects with limited time or budget constraints.
- Limitations: The accuracy of the model depends on the quality and coverage of the photographs. Additionally, the resulting model is less flexible for edits once it has been generated, making it less suitable for iterative design processes.
- Common Use Cases:
- Object Digitization: Creates detailed, accurate digital replicas of real-world objects for study or display.
- Budget-Friendly Applications: Ideal for projects requiring precise but low-cost 3D models, such as educational or prototype projects.
- Virtual Museums: Used to create digital replicas of museum exhibits for online or virtual experiences.
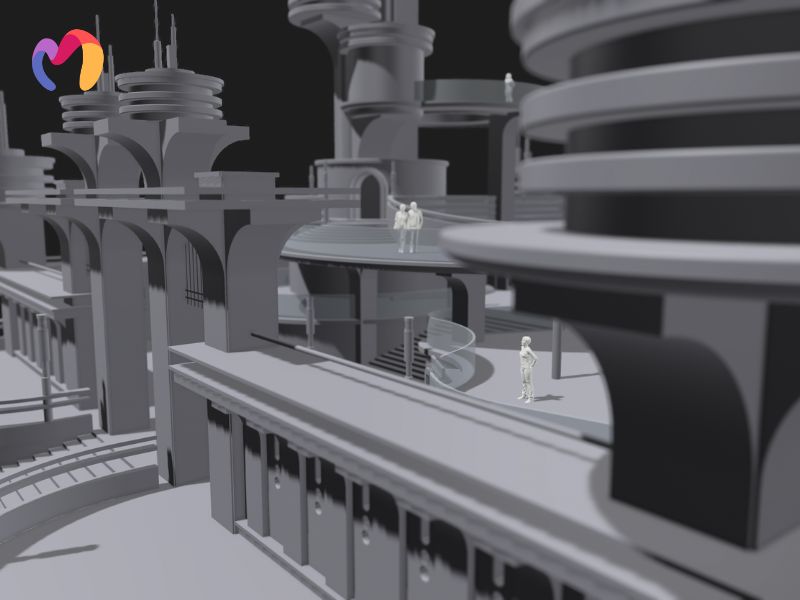
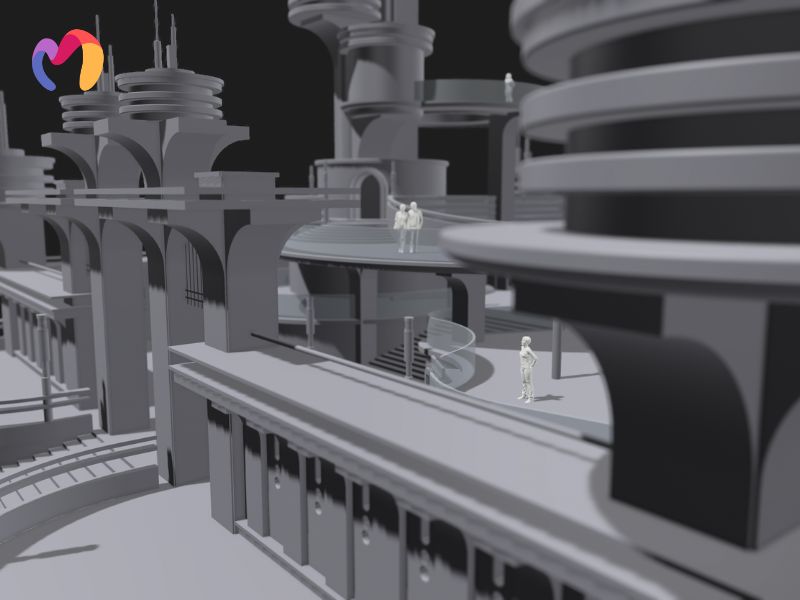
2. How to choose the Right 3D Modeling Technique
When selecting a 3D modeling technique, consider factors like project goals, precision needs, software tools, and available resources. The technique should align with the project’s requirements, whether it’s for precise manufacturing or high-quality visualization. Matching the method to both technical and practical constraints ensures efficient workflows and successful outcomes.
2.1. Factors to Consider in Technique Selection
3D modeling technique selection depends on core elements that shape project success:
- Project Complexity: Workflow needs drive modeling methods, feature density determines the approach, and structure hierarchy impacts tool selection.
- Resources and Time: Budget limits define tool options, deadlines shape process choices, and team size affects workflow speed.
- Detail Requirements: Mesh density matches output goals, precision needs guide tool picks, and surface quality drives polygon count.
- Technical Limitations: Hardware power sets boundaries, software features control options, and memory constraints affect scale.
2.2. Industry-Specific 3D Modeling Requirements
Each industry demands specific 3D modeling methods to meet functional requirements and production standards.
Industry | Preferred Techniques | Reasons for Preference | Examples of Applications |
Architecture | NURBS, Solid Modeling | Requires precision and spatial accuracy for building design | Structural blueprints, building analysis |
Gaming | Polygonal Modeling | Needs optimization for performance and real-time rendering | Character modeling, game world environments |
Manufacturing | CAD, Parametric Design | Demands technical accuracy and production readiness | Product development, machine tools, prototyping |
Medical | Surface Modeling | Focuses on bio-accuracy and functional design for medical tools | Medical device design, anatomical modeling |
Film/Animation | Subdivision Surface Modeling | Prioritizes visual appeal and fluid movement for animation | Character animation, special effects in films
|
3. Frequently Asked Questions About 3D Modeling
How to create a 3D model?
To create a 3D model, follow these steps:
- Start with a basic shape (cube, sphere, etc.).
- Add more detail by sculpting or extruding.
- Refine geometry and ensure correct proportions.
- Apply textures and materials for realism.
- Use lighting and cameras for rendering.
- Export the model in a preferred format.
How to change the file type of a 3d model?
To change the file type of a 3D model, follow these steps:
- Open the model in your 3D modeling software.
- Go to the File menu and select Export or Save As.
- Choose the desired file format (e.g., STL, OBJ, FBX, etc.).
- Adjust any export settings, such as scale or texture options, if necessary.
- Save the model in the new file format.
What file formats are used in 3D modeling?
Common file formats in 3D modeling include STL (for 3D printing), OBJ (used for textures and meshes), FBX (for animations and 3D assets), and DAE (used for web-based applications). These formats are essential for sharing models between software and platforms.
Conclusion
Understanding the 11 distinct types of 3D modeling is crucial for selecting the appropriate method for your project. From basic Wireframe Modeling to complex NURBS Modeling, each technique offers unique advantages and applications across various design and architectural fields.
3DMAXTER specializes in providing professional 3D modeling services for architects and interior designers. With our team of experienced specialists, we help you select and implement the most suitable modeling approach for your project. Contact us today for detailed consultations and competitive quotes on our comprehensive 3D modeling services.
3DMAXTER LTD
- Email: [email protected]
- Phone: +1 (929) 450-2898
- Address: 95-38 Queens Blvd, Rego Park, NY 11374, USA
Thank you for choosing 3DMAXTER LTD.