3D printing, also known as additive manufacturing, is the process of creating three-dimensional objects from a digital file by building them layer by layer. If you’re wondering what is 3D printing exactly, it’s a revolutionary technology that transforms digital designs into physical items using materials like plastic, resin, or metal. From prototyping to manufacturing, 3D printing is reshaping industries and opening up new possibilities for innovation and customization. In this article, we’ll break down how 3D printing works, explore its main technologies, and look at real-world applications.
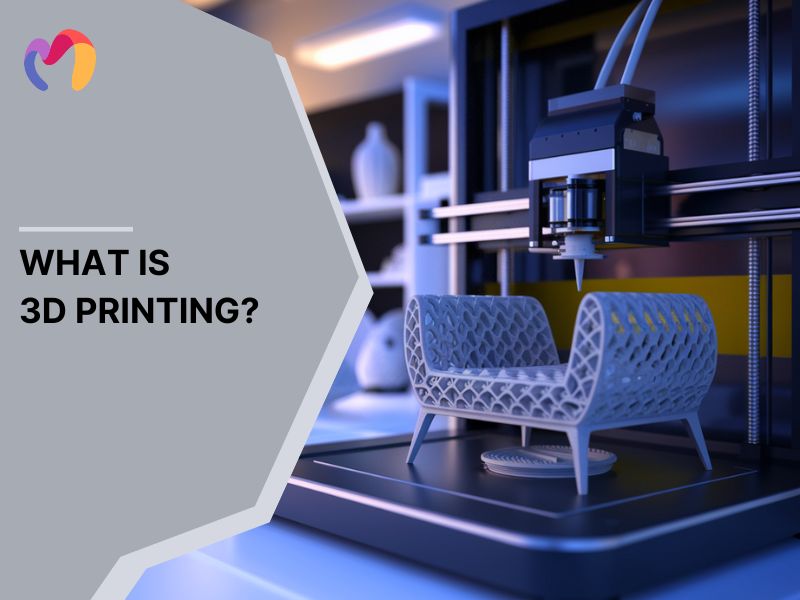
What is 3D Printing?
3D printing is an innovative fabrication method that builds physical objects directly from digital designs by adding material rather than removing it. In architectural and interior design contexts, this technology has become a powerful tool for translating creative concepts into tangible forms with unprecedented precision and design freedom.
Unlike traditional model-making or manufacturing processes that rely on cutting, carving, or molding, 3D printing constructs objects layer by layer according to detailed digital specifications. Architects and designers can produce complex scale models, custom fixtures, furniture prototypes, and decorative elements that would be extremely difficult to create using conventional methods.
The process begins with a digital 3D model—often created in industry-standard CAD or BIM software used by design professionals. This model is then processed by “slicing” software that divides it into hundreds of horizontal cross-sections and generates instructions for the printer. The printer executes these commands by systematically building the object from bottom to top, with each new layer bonding to the previous one.
For architecture and interior design applications, 3D printing offers remarkable advantages: the ability to produce intricate organic forms, rapid iteration of design concepts, creation of custom elements tailored to specific spaces, and visualization of complex spatial relationships through accurate physical models. This technology is reshaping how design professionals communicate ideas, test solutions, and deliver unique, customized elements for their projects
>>> See more: 5 Most Common 3D Printing File Types In 2025
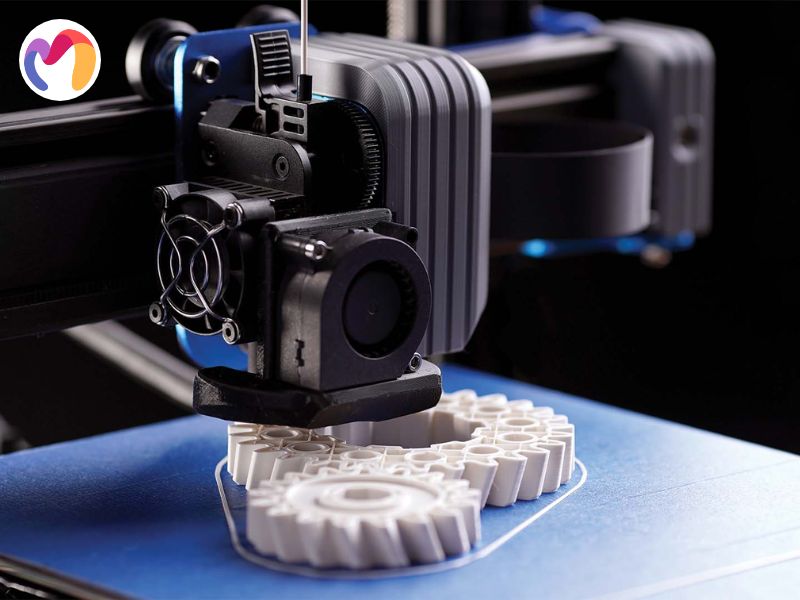
Advantages and Disadvantages of 3D Printing
3D printing is transforming manufacturing by enabling new production methods across multiple industries. To leverage its full potential, it is essential to understand both its advantages and constraints.
5 Advantages of 3D Printing
3D printing technology is revolutionizing manufacturing by optimizing designs, reducing costs, and accelerating product development. Here are five key benefits of 3D printing:
- Customization and On-Demand Production: 3D printing, an additive manufacturing technique, enables the creation of custom-designed components tailored to unique specifications. This is crucial for industries like healthcare (prosthetics, implants), architecture (scale models), and industrial manufacturing (automotive, aerospace).
- Rapid Prototyping and Product Development: Companies can iterate designs efficiently by producing and testing prototypes without large-scale manufacturing commitments. This process minimizes reliance on traditional factory setups and optimizes supply chains.
- Material Efficiency and Waste Reduction: Unlike subtractive methods, which remove excess material, 3D printing utilizes only what is necessary. This precision is particularly valuable for high-cost materials like rare metals and advanced composites.
- Decentralized Manufacturing and Inventory Optimization: On-demand production reduces the need for extensive warehousing. Businesses can fabricate spare parts when required, lowering storage costs and improving supply chain agility.
- Complex Geometries and Enhanced Design Flexibility: 3D printing enables intricate structures, including lattice frameworks and internal cavities, that traditional manufacturing struggles to achieve. This capability enhances component strength-to-weight ratios, benefiting sectors such as aerospace and biomedical engineering.
>> See more: 8 Transformative Benefits of Architecture 3D Models
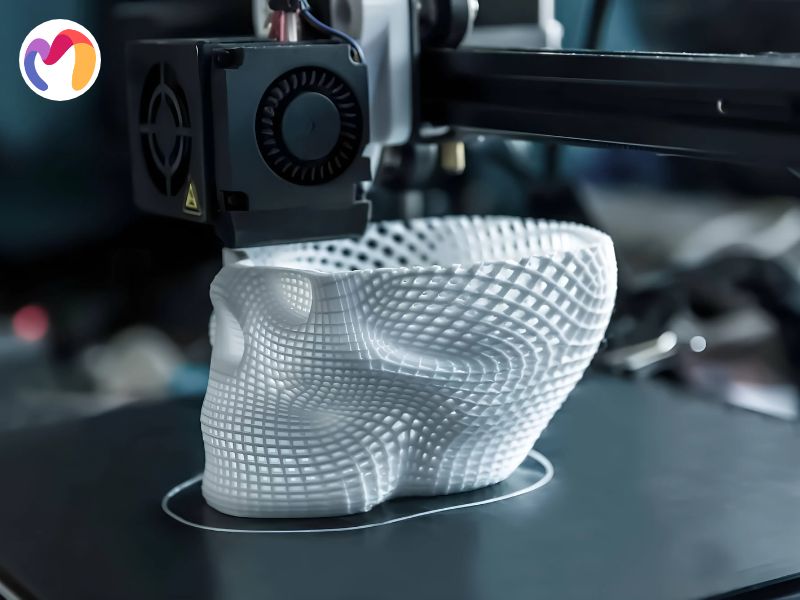
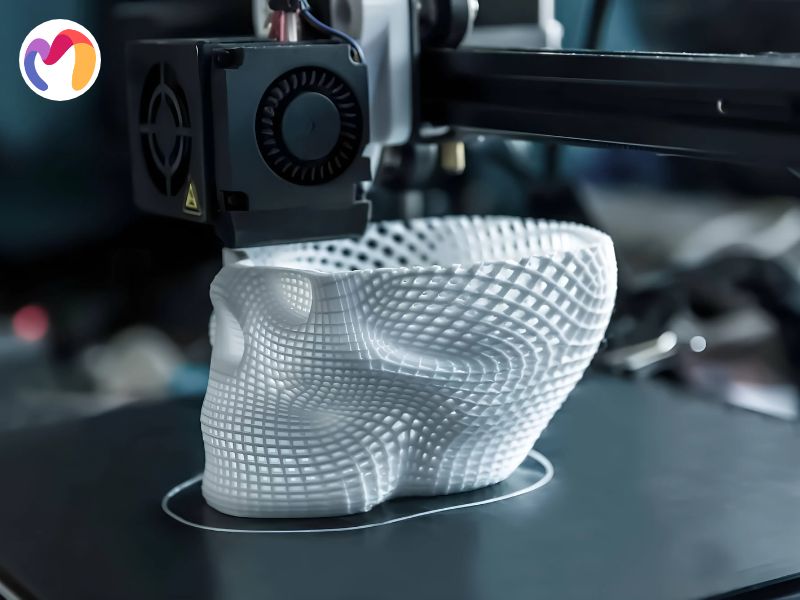
5 Disadvantages of 3D Printing
While 3D printing offers significant benefits, it also presents several challenges that impact its scalability, efficiency, and security. Below are five key limitations:
- Material Constraints: The selection of materials suitable for 3D printing remains narrow compared to traditional manufacturing. While polymers and metals are commonly used, many industrial applications require materials with specialized mechanical properties, thermal resistance, or durability that additive manufacturing has yet to support efficiently.
- Production Speed and Scalability: Despite its precision, additive manufacturing relies on a layer-by-layer process that is time-intensive. Complex geometries and large-scale objects further extend production times, making 3D printing less viable for high-volume manufacturing. Conventional methods like injection molding or CNC machining are often more efficient for mass production.
- High Initial Investment: Advanced 3D printers, particularly those used for industrial applications, require substantial capital expenditure. In addition to the cost of the machine, expenses include proprietary materials, periodic maintenance, and software licenses. These factors contribute to a high total cost of ownership, limiting accessibility for smaller enterprises.
- Post-Processing Requirements: Printed components frequently require post-processing to achieve the desired finish and functionality. This includes support removal, surface refinement, and additional coatings. These extra steps introduce additional labor and costs, offsetting some of the efficiencies gained through the printing process.
- Intellectual Property and Security Risks: The digital nature of 3D printing exposes businesses to intellectual property vulnerabilities. CAD files can be copied, shared, or modified with minimal oversight, increasing the risk of design theft and counterfeit production. Implementing encryption, watermarking, and cybersecurity protocols is necessary to safeguard proprietary models.
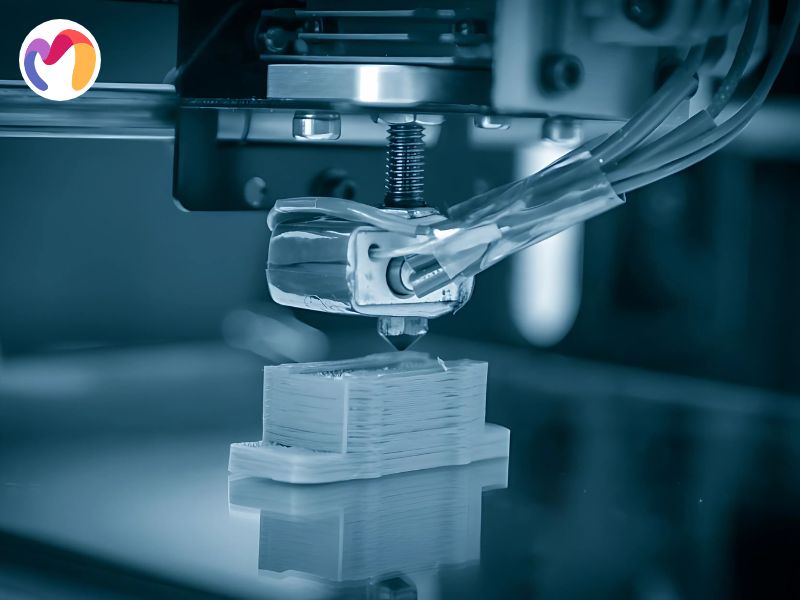
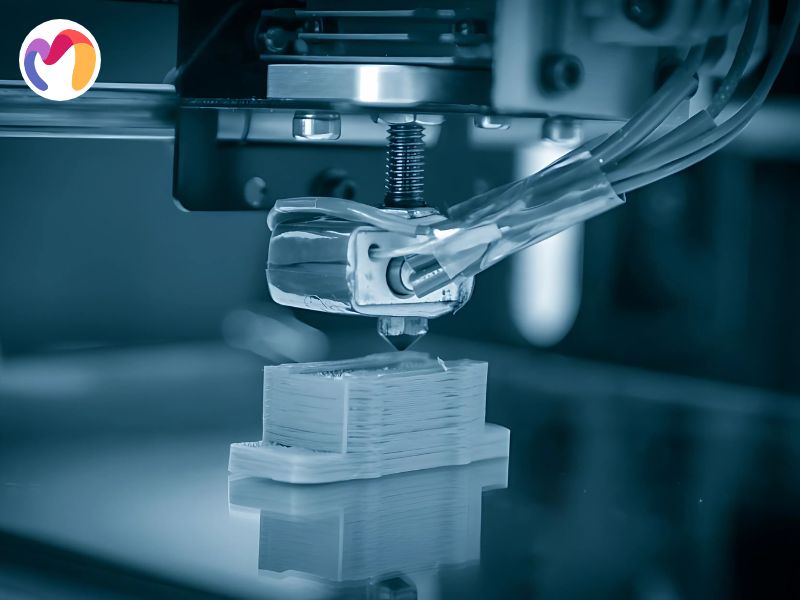
How Do 3D Printings Work?
3D printing follows a four-step process, converting digital designs into physical objects through additive manufacturing.
Step 1: Creating the 3D Model
Design begins in CAD software, from beginner-friendly Tinkercad to advanced tools like Fusion 360 and Blender. The model must suit printing constraints—wall thickness, support structures, and orientation—to ensure success. Understanding layer adhesion, material limits, and overhang tolerances reduces failures and strengthens prints.
Step 2: Slicing and G-Code Generation
Once finalized, the model is sliced into horizontal layers and converted into G-code, a set of commands for the printer. Key parameters include:
- Infill Density – Controls internal structure, balancing strength and material use.
- Support Structures – Stabilize overhangs to prevent collapse.
- Adhesion Methods – Rafts, brims, or skirts improve bed adhesion and prevent warping.
Optimizing these settings affects print quality, speed, and efficiency.
Step 3: Printing Layer by Layer
With G-code loaded, the printer builds the object. In FDM, a heated nozzle extrudes melted filament, depositing material layer by layer. In SLA, a laser cures liquid resin to form solid layers. Temperature control and print speed ensure proper bonding, structural integrity, and surface quality. Infill patterns, like honeycomb or grid, optimize strength while conserving material.
Step 4: Post-Processing
After printing, refinements enhance durability and appearance:
- Support Removal – Detaching temporary structures without damage.
- Surface Treatment – Sanding, polishing, or chemical smoothing (e.g., acetone vapor for ABS).
- Additional Processing – Painting, coating, or reinforcing for added strength.
Industrial applications may include heat treatments or composite reinforcement to improve mechanical properties.
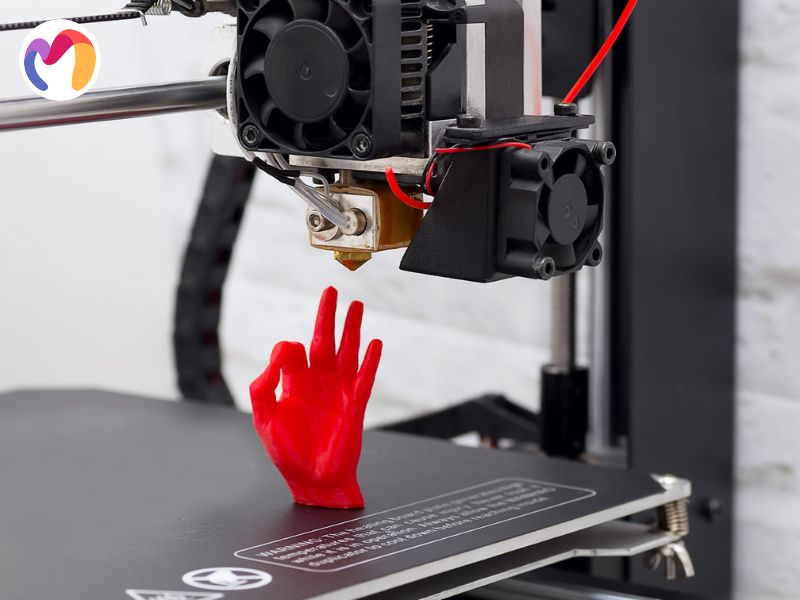
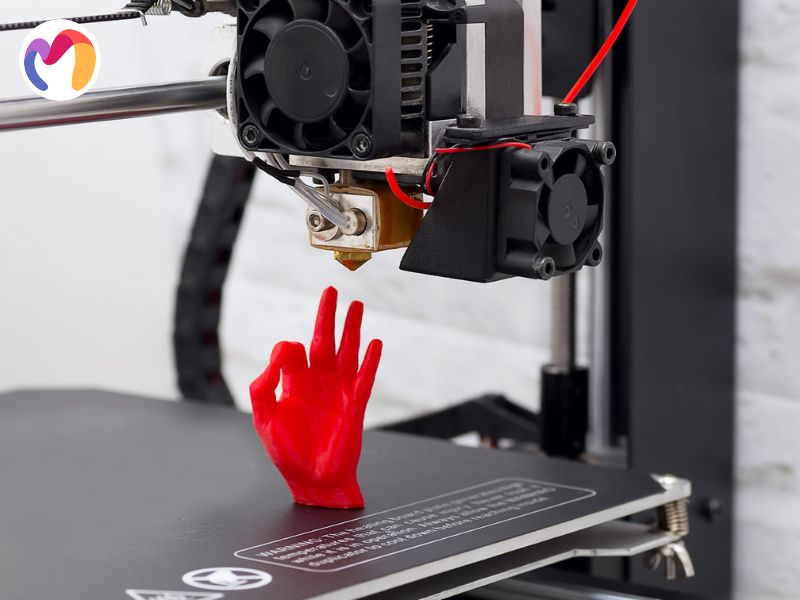
4 Types of 3D Printing Technologies
Modern manufacturing relies on four key 3D printing methods: Fused Deposition Modeling (FDM), Stereolithography (SLA), Selective Laser Sintering (SLS), and Digital Light Processing (DLP). Each serves distinct needs in cost, precision, and material use.
Fused Deposition Modeling (FDM): Affordable and Versatile
FDM fabricates 3D objects by depositing molten thermoplastic filament through a precisely controlled nozzle, layer by layer. The process resembles a mechanized extrusion system, where material solidifies to form a structured model.
Advantages:
- Entry-level FDM printers are accessible from $300, making them a preferred choice for prototyping and academic applications.
- Users control infill percentage to optimize mechanical properties while minimizing material consumption.
- Compatible with PLA, ABS, PETG, and reinforced composites, allowing tailored material selection for functional requirements.
Disadvantages:
- Visible layer lines necessitate post-processing such as sanding or solvent-based smoothing to enhance finish quality.
- Limited mechanical strength compared to metals or advanced high-performance polymers, restricting application in high-stress environments.
Stereolithography (SLA): High-Detail Resin Printing
Stereolithography (SLA) is an additive manufacturing process that utilizes a UV laser to cure liquid photopolymer resin layer by layer, forming highly detailed and precise 3D prints. It is widely used for applications requiring intricate features and smooth surfaces.
Advantages:
- Achieves fine resolutions, making it ideal for dental models, jewelry, and high-fidelity prototypes.
- Produces near-polished finishes, reducing the need for extensive post-processing.
- Offers resins with varied properties, including flexibility, impact resistance, high-temperature endurance, and biocompatibility for medical use.
Disadvantages:
- SLA printers and specialized resins are more expensive than FDM counterparts.
- Prints must be cleaned with isopropyl alcohol and cured under UV light for optimal strength.
Selective Laser Sintering (SLS): Industrial-Grade Powder Printing
SLS employs a high-energy laser to thermally bond polymer or metal powders layer by layer, enabling the fabrication of intricate, high-strength parts without external support structures.
Advantages:
- The surrounding powder functions as an inherent support system, eliminating the need for additional scaffolding.
- SLS produces durable components suitable for aerospace, automotive, and medical applications, where mechanical integrity is critical.
- The process facilitates simultaneous printing of multiple parts, optimizing throughput and material utilization.
Disadvantages:
- SLS demands specialized industrial-grade hardware, making initial investment and maintenance substantial.
- Printed parts require powder removal, surface refinement, and optional finishing techniques such as dyeing or polishing to meet application-specific standards
Digital Light Processing (DLP): Fast and Precise Resin Printing
DLP utilizes a digital micromirror device (DMD) to project ultraviolet (UV) light across an entire resin layer, curing it simultaneously. Unlike Stereolithography (SLA), which traces each layer point-by-point with a laser, DLP accelerates the printing process without sacrificing detail.
Advantages:
- By solidifying full layers in one exposure, DLP prints faster than SLA.
- Achieves layer thickness as fine as 30 microns, enabling sharp features and intricate geometries.
- Popular in dental prosthetics, hearing aids, jewelry casting, and engineering prototypes requiring micron-level accuracy.
Disadvantages:
- Best for compact, detail-intensive parts rather than large models.
- Material options, while expanding, are more limited than SLA and FDM.
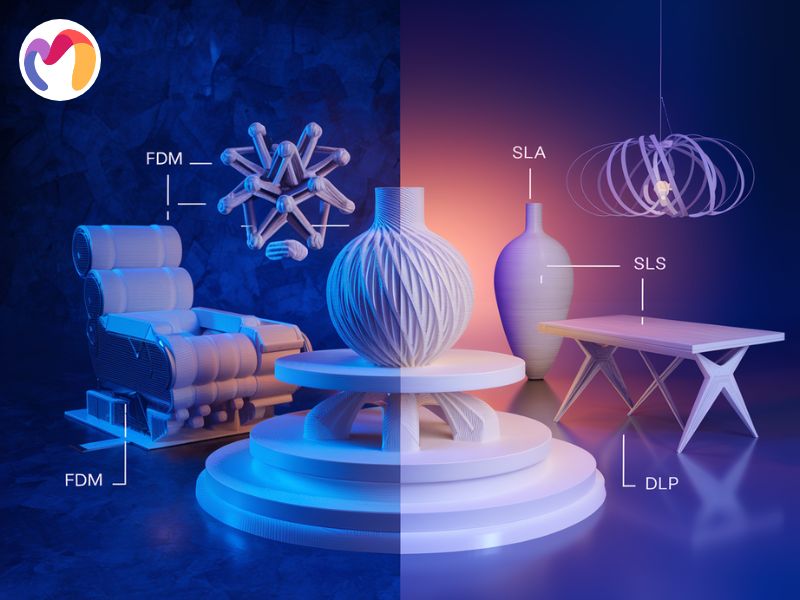
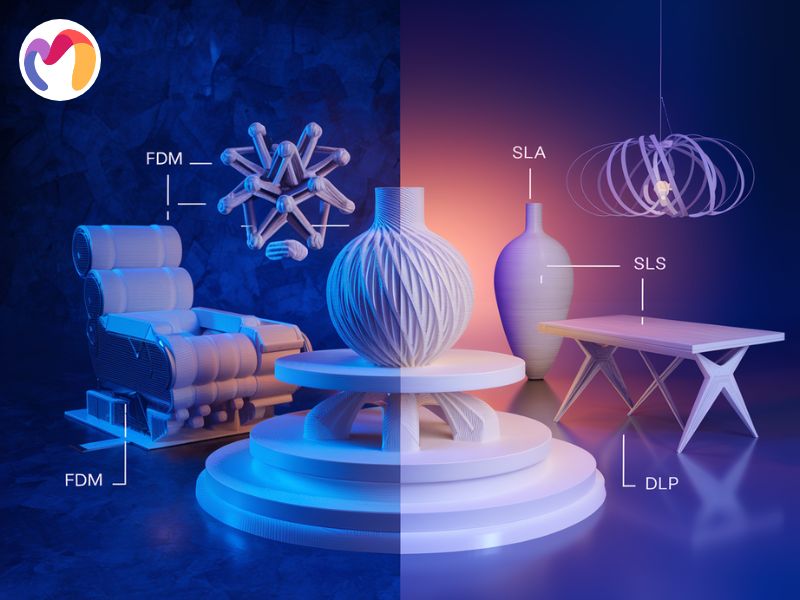
3 Materials Used in 3D Printing: A Diverse Palette
3D printing relies on three primary material types: filaments, resins, and powders. Each serves distinct applications, from prototypes to functional components.
Filament Materials: Accessible and Versatile
FDM (Fused Deposition Modeling) printers use thermoplastic filaments that are melted and extruded layer by layer. For architectural applications, these materials offer practical benefits in model-making and prototype development.
PLA (Polylactic Acid) provides excellent detail for conceptual models and is biodegradable, supporting sustainable design practices. ABS (Acrylonitrile Butadiene Styrene) offers superior durability for functional prototypes that require handling. PETG combines ease of printing with greater strength, ideal for sectional models or custom hardware prototypes.
Resin-Based Materials: High-Detail Printing
SLA (Stereolithography) and DLP (Digital Light Processing) technologies utilize liquid photopolymer resins cured by light to create highly detailed objects. For architectural visualization, standard resins achieve exceptional surface finish and fine detail reproduction, perfect for complex façade studies and intricate interior elements.
Specialized architectural resins include transparent varieties for simulating glass elements and flexible formulations for components requiring elasticity such as landscape topography or ergonomic furniture prototypes. Engineering resins with ceramic-like or heat-resistant properties enable the creation of durable presentation models and functional prototypes for custom fixtures.
Powder-Based Materials: Industrial-Grade Strength
Powder-based printing methods like SLS (Selective Laser Sintering) fuse materials layer by layer using lasers, offering advantages for advanced architectural applications. Nylon powders produce strong, flexible components ideal for interlocking or mechanically functional elements in architectural models.
Metal powders including aluminum, titanium, and stainless steel allow for the fabrication of structural components, custom hardware, and high-end decorative elements with exceptional strength-to-weight ratios. Specialized architectural powders include gypsum composites that create full-color conceptual models and sandstone materials that emulate the appearance and texture of traditional architectural materials, enhancing presentation quality.
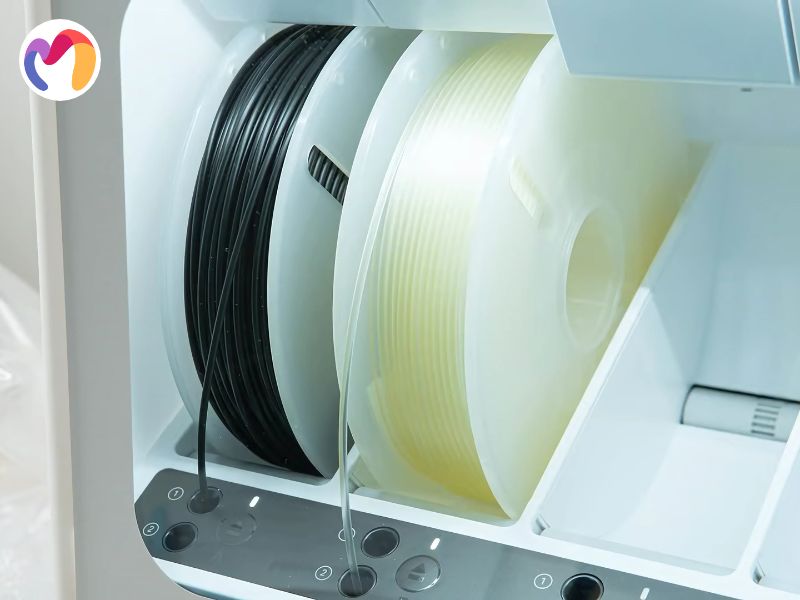
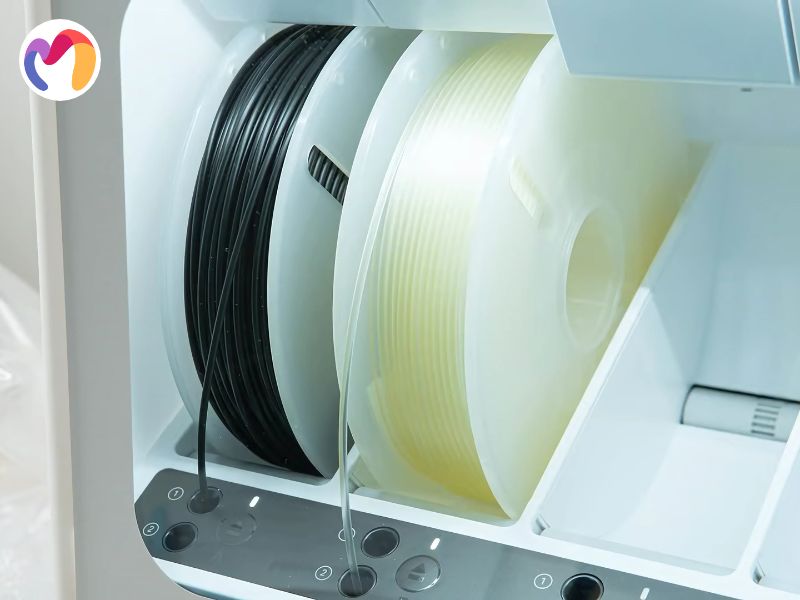
Applications of 3D Printing Across Industries
3D printing is transforming manufacturing, healthcare, construction, aerospace, and automotive sectors. It enables rapid prototyping, custom fabrication, and efficient production of complex components.
- Manufacturing: Rapid Prototyping and Custom Parts:Â 3D printing accelerates product development by allowing engineers to prototype and test designs in days instead of weeks. Manufacturers print discontinued parts for classic vehicles, solving supply shortages. Aerospace companies use 3D-printed turbine frames and fuel injectors to cut weight and reduce material waste. This technology eliminates excess inventory by enabling just-in-time production.
- Medicine: Revolutionizing Healthcare with Personalized Solutions: Doctors use 3D printing to create patient-specific implants, prosthetics, and surgical models. Custom prosthetics improve fit and function. Over 100,000 hip implants have been 3D printed, proving the technology’s reliability. Bioprinting research explores ways to fabricate living tissues, with future applications in organ transplants. Dentists print crowns, dentures, and aligners with greater precision and lower costs.
- Architecture and Construction: Building the Future:Â 3D printing speeds up construction and reduces material waste. Printed homes lower costs and cut build times. Specialized concrete ensures strength while allowing flexible designs. Architects use 3D printing to create detailed models, improving project planning and execution. This technology minimizes labor costs and expands design possibilities.
- Aerospace and Automotive: Lightweight and Complex Parts:Â 3D printing produces lighter, stronger components. Aircraft manufacturers use printed fuel injectors to improve performance. Car companies print custom and obsolete parts, resolving supply chain delays. Engineers refine designs without expensive tooling changes, making innovation faster and cheaper.
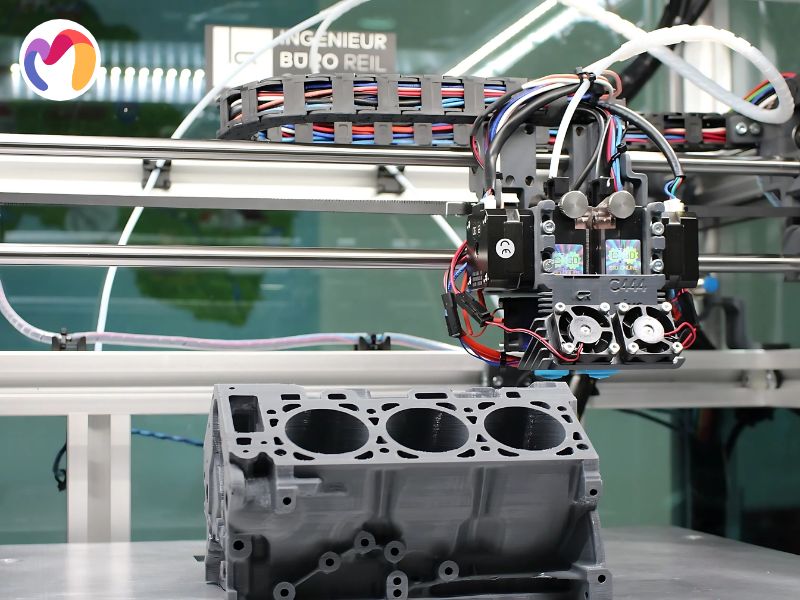
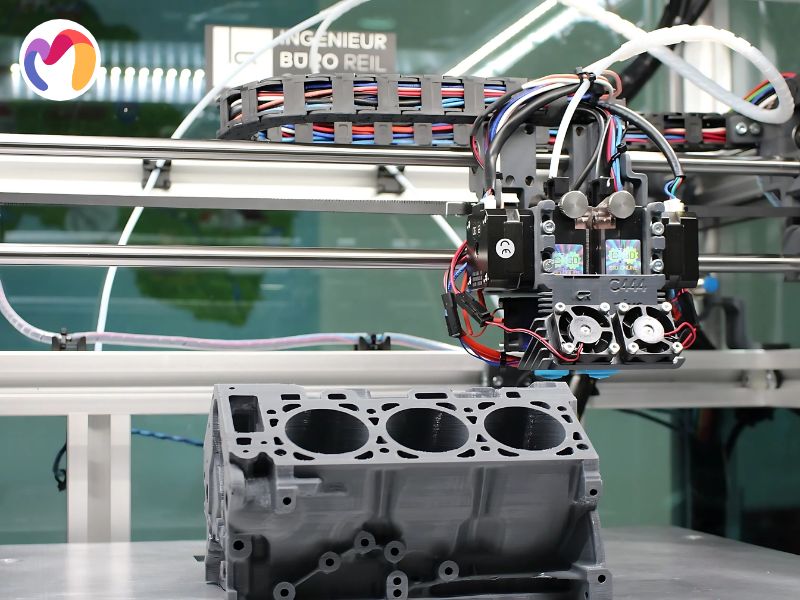
Environmental Implications of 3D Printing
3D printing reshapes manufacturing’s environmental impact by reducing waste, optimizing energy use, and enabling sustainable materials.
Reducing Waste Through Additive Manufacturing
Unlike traditional methods that cut away material, 3D printing builds objects layer by layer, minimizing waste, including:
- Conventional machining wastes up to 90% of material, while 3D printing uses only slightly more than required.
- Support structures and failed prints can be reused.
- Adidas turns ocean plastic into 3D-printed shoe soles, and construction firms reduce concrete waste through precise deposition.
Energy Consumption: A Comparative Analysis
Energy use in 3D printing depends on material, machine efficiency, and production scale. Let’s compare the two approaches:
Traditional Manufacturing | 3D Printing |
High energy for large batches | Energy scales with part size |
Constant power for machinery | Power used only when printing |
Heavy facility requirements | Minimal facility needs |
High transport energy costs | Local production reduces transport |
Fixed energy per unit | Variable energy per design |
3D printing uses less power for low-volume, complex parts. Mass production, however, remains more energy-efficient with conventional methods. Advances in print path optimization and thermal management now cut 3D printing energy use by up to 50%. By reducing transport needs and optimizing energy, 3D printing improves sustainability.
Sustainable Materials in 3D Printing
3D printing supports sustainability by using eco-friendly materials instead of petroleum-based plastics. Bio-based filaments like PLA come from renewable sources such as corn starch and cellulose. Recycled plastics repurpose industrial and consumer waste, reducing landfill impact. Biodegradable resins, derived from soy, algae, and plant oils, further minimize environmental harm. These materials promote a circular economy, making 3D printing a greener manufacturing solution.
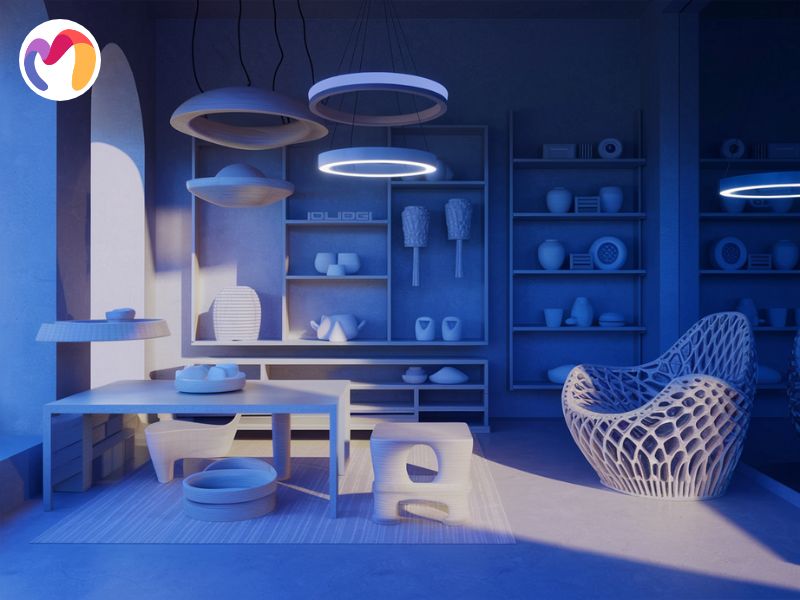
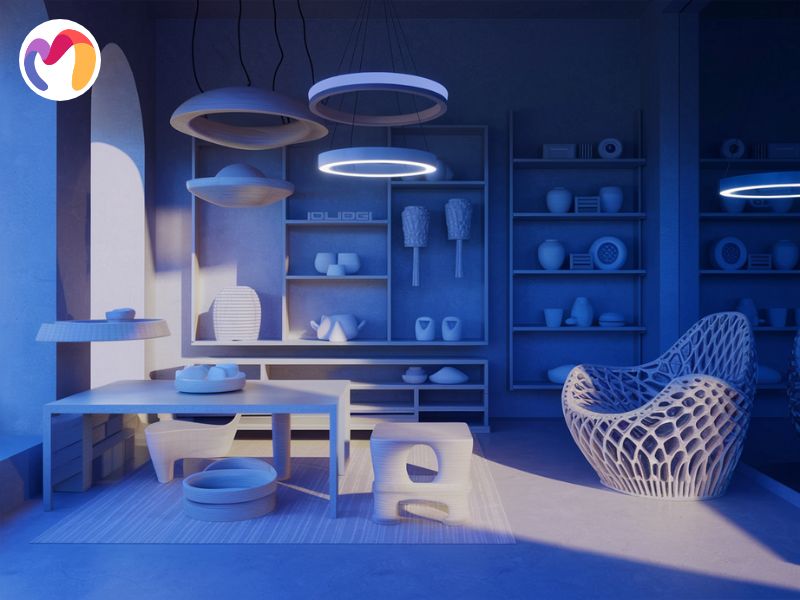
Frequently Asked Questions About 3D Printing
Is 3D printing expensive?
Yes. Costs vary based on printer type, materials, and object complexity. Entry-level printers start at $300, while industrial models exceed $100,000. Materials like plastics are cheap, but metals and specialized materials are costly.
What’s the difference between 3D printing and CNC machining?
Understanding key differences between 3D printing and CNC machining helps makers choose the right manufacturing method for their projects.
- 3D Printing: Builds objects layer by layer. Best for complex shapes, low waste, and small batches. Slower but cheaper upfront.
- CNC Machining: Removes material from a solid block. Offers high precision and speed but generates more waste. Ideal for mass production.
Both methods complement each other in modern manufacturing.
Can 3D printing be used for mass production?
No, traditional 3D printing is slow, but new technologies like volumetric printing and hybrid manufacturing are making large-scale production viable. Companies like Adidas use 3D printing for mass customization. It’s not yet a full replacement for traditional manufacturing but is effective for complex, low-volume parts.
How does 3D printing impact intellectual property rights?
3D printing makes copying designs easier, challenging IP protection. CAD files can be shared and reproduced without permission. Solutions include digital rights management (DRM), encrypted design files, and legal updates to regulate unauthorized reproduction. Protecting IP in 3D printing requires both legal and technological measures.
Conclusion
3D printing redefines manufacturing by enabling complex designs, efficient production, and tailored solutions across industries. It bridges the gap between prototyping and full-scale production, driving innovation in healthcare, construction, aerospace, and beyond.
Challenges remain, but advancements in sustainable materials, energy efficiency, and scalability push the technology forward. The future of additive manufacturing lies in greener processes, smarter automation, and wider accessibility. For deeper insights, explore our blog or browse optimized 3D models at 3DMAXTER.
3DMAXTER LTD
- Email: [email protected]
- Phone: +1 (929) 450-2898
- Address: 95-38 Queens Blvd, Rego Park, NY 11374, USA
Thank you for choosing 3DMAXTER