The 3D modeling workflow represents a carefully structured approach that transforms abstract concepts into visually stunning digital assets. This methodical process combines technical expertise with creative vision to ensure consistent quality and efficient production across architectural visualizations, product designs, and digital environments.
Our comprehensive guide breaks down the professional 3D modeling workflow into 8 essential steps, each building upon the previous to create a seamless progression from concept to completion. By understanding and implementing this systematic approach, you’ll elevate your 3D modeling projects, optimize your production pipeline, and deliver exceptional results that meet the highest standards of quality and performance in the competitive 3D visualization marketplace.
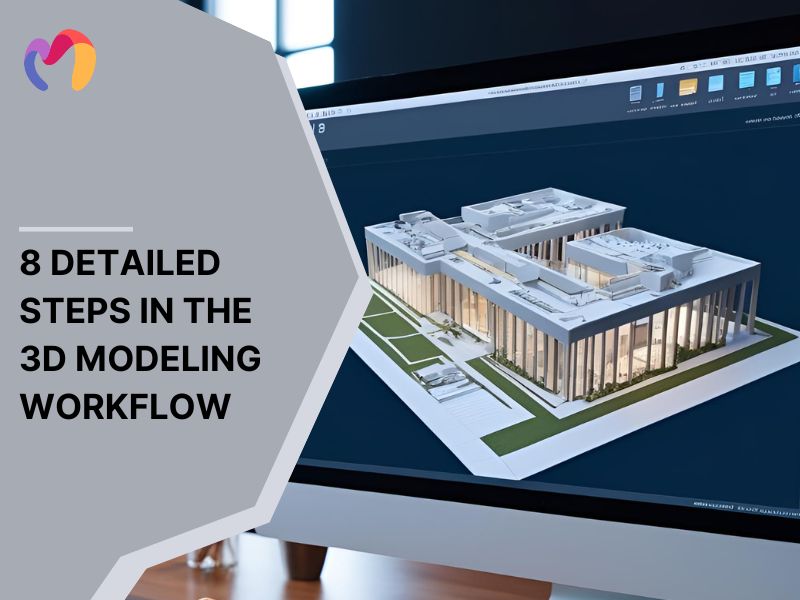
Step 1. Initial Planning and Conceptualization
A successful 3D modeling project starts with thorough preparation. This phase involves gathering references, defining project scope, and ensuring clear communication with clients to align expectations and technical requirements.
Gathering References and Inspiration
To create accurate 3D models, you need to collect reference materials organized into different categories for efficient access:
- Primary references: Essential images, drawings, and models directly related to the project
- Secondary references: Additional details that enhance realism or accuracy
- Technical references: Design blueprints, specifications, polygon limits, and texture requirements
- Inspiration references: Artistic direction and stylistic influences
Defining Project Scope and Objectives
Establishing clear scope and objectives prevents misalignment and scope creep. Key considerations include:
- Deliverables (model types, detail levels, file formats)
- Technical specifications (polygon count, UV mapping, texture resolution)
- Budget and timeline with measurable milestones for tracking progress
Client Communication and Requirement Analysis
You should follow a three-step process: Initial consultation to understand the vision, detailed analysis to document requirements, and clarification to refine. Areas of focus include scope, file formats, timelines, and budget planning, supported by project management tools and regular updates.
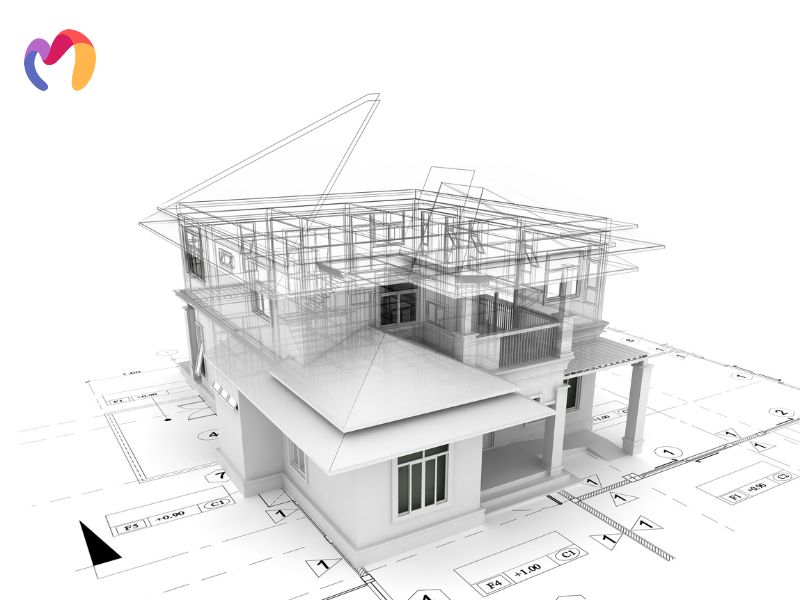
Step 2. Blocking and Basic Shape Creation
Blocking is the foundation of 3D modeling. It establishes form, proportion, and silhouette using basic geometric shapes. This stage in 3D modeling workflow defines the model’s structure before adding finer details, ensuring a solid framework for further refinement.
Using Primitive Shapes for Initial Blocking
3D models begin with simple shapes that form the foundation for complex structures:
- Spheres for heads and rounded body parts
- Cylinders for limbs, pipes, and tubular structures
- Cubes for torsos, architectural elements, and mechanical parts
- Cones for pointed features and organic transitions
- Planes for flat surfaces and background elements
Establishing Proportions and Silhouettes
Correct proportions ensure balance and realism. You can verify proportions using orthographic views, reference alignments, grid snapping, and silhouette checks from various angles to maintain consistency and prevent distortion.
Refining Basic Forms and Structures
You can strengthen the model’s structure through edge loops for controlled curvature, support edges for defined contours, and adjusted mesh density for detailed areas.
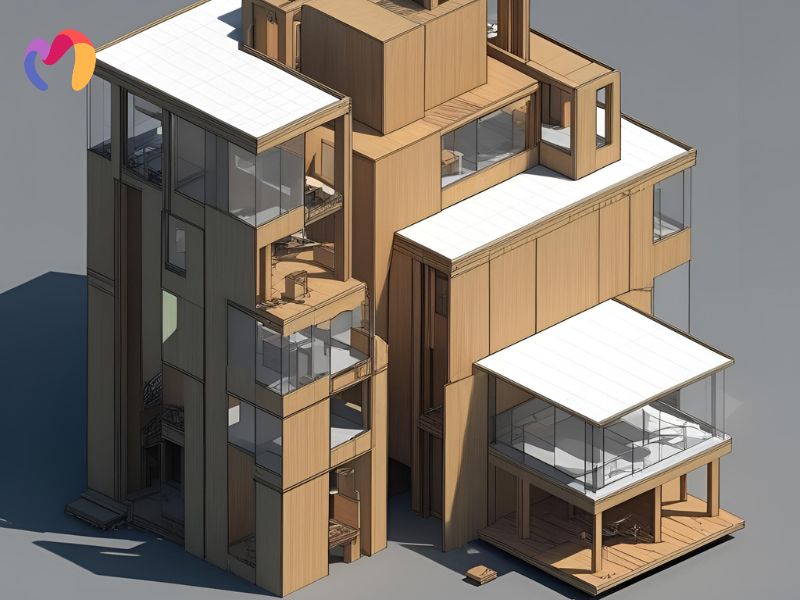
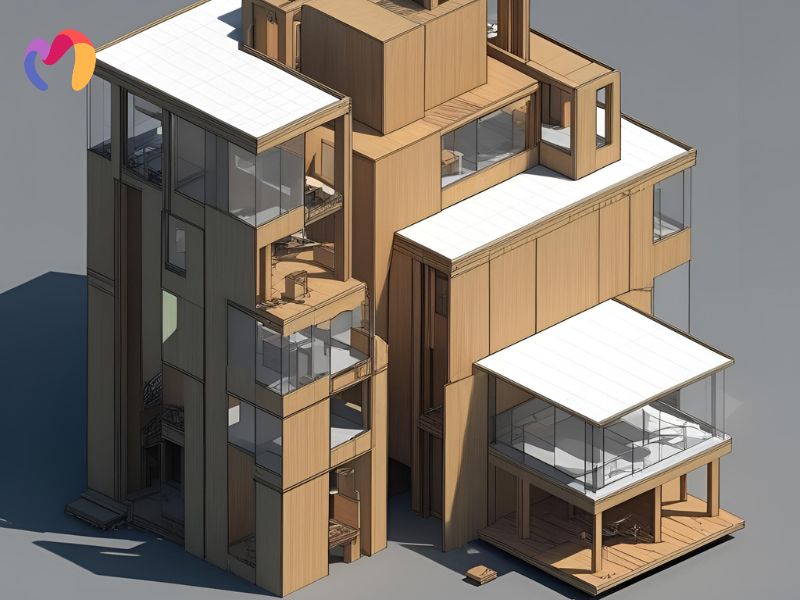
Step 3. Detailed Modeling Techniques
Detailed modeling refines a 3D model’s structure by balancing efficiency and realism. The process starts with low-poly modeling to establish form, then advances to high-poly sculpting for intricate details. This 3D modeling workflow ensures adaptability across applications while maintaining artistic depth.
Low-Poly Modeling: Building the Basics
This approach optimizes performance using simplified geometry. Key techniques include breaking complex forms into basic structures, ensuring clean topology, positioning edge loops, and reducing unnecessary geometry while maintaining critical details.
High-Poly Sculpting: Adding Fine Details
Digital sculpting enhances models with organic surfaces and textures using dynamic subdivision, mask-based sculpting, alpha brushes, and surface smoothing. Programs like ZBrush and Blender offer tools for non-destructive workflows with symmetry and layering.
>>> Discover more: What Is The Difference Between Low Poly and High Poly in 3D Modeling?
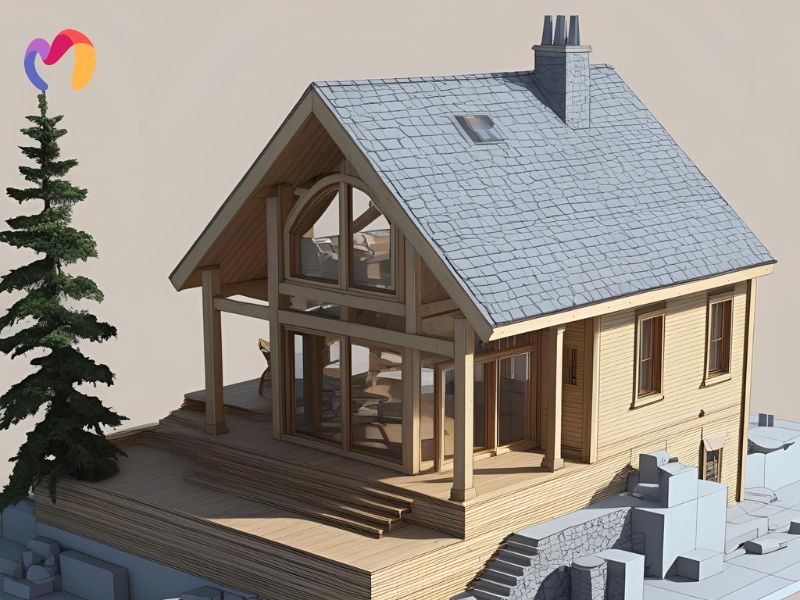
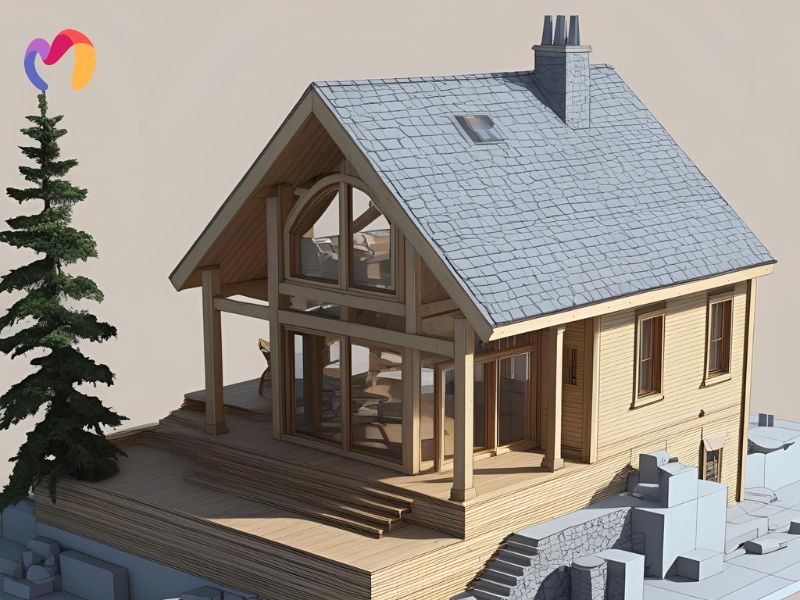
Step 4. Texture Mapping and UV Unwrapping
Texture mapping begins with UV unwrapping, a process that converts a 3D model’s surface into a 2D layout. This allows textures to align correctly, preventing distortion and preserving visual fidelity. Proper UV mapping enhances model realism by ensuring accurate placement of colors, roughness, reflections, and surface details.
- Understanding UV Coordinates: UV coordinates guide texture placement, with “U” running horizontally and “V” vertically. Each 3D face aligns with a corresponding 2D texture section, using UV layout diagrams with visible grids to detect misalignment.
- Efficient UV Unwrapping Techniques: Techniques include planar mapping for flat surfaces, cylindrical mapping for round objects, spherical mapping for spherical shapes, and automatic unwrapping for complex models. Best practices include consistent texel density, strategic seam placement, and efficient UV island organization.
- Creating and Applying Textures: Texturing defines surface characteristics using albedo (color), normal (detail), roughness (smoothness), metallic, and ambient occlusion maps. The process follows a structured workflow from UV application through base colors and detail maps to final export.
>>> See more: What Is 3D Texturing? A Comprehensive Guide to Enhancing 3D Models
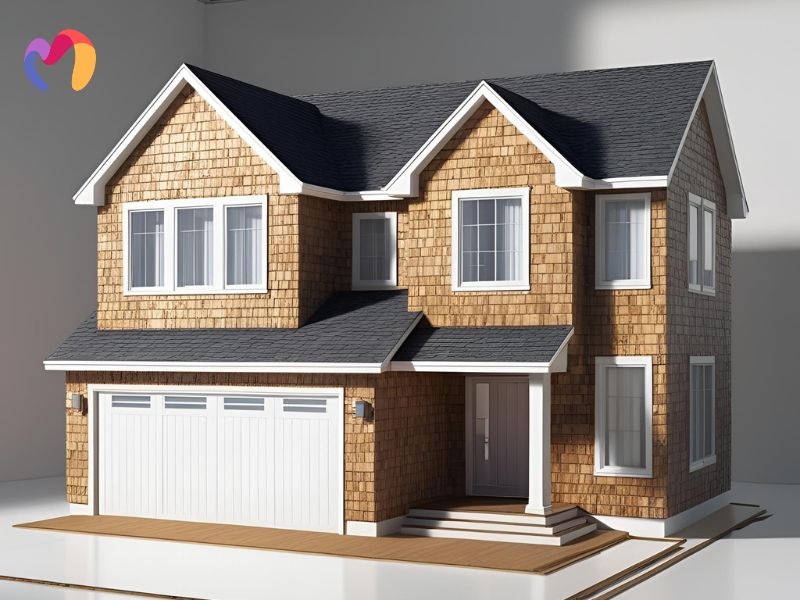
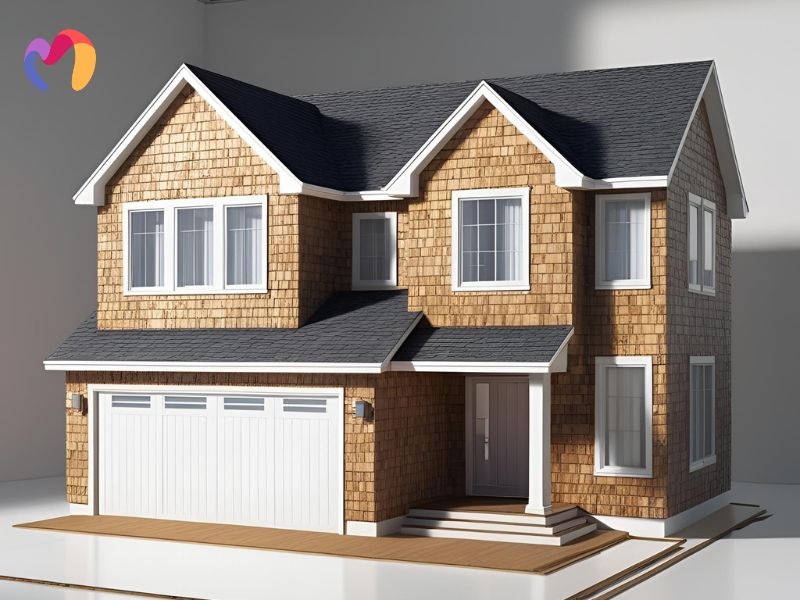
Step 5. Materials and Shading
In 3D modeling workflow, materials and shaders define how your 3D models interact with light, influencing their surface properties, from reflection to transparency. By controlling shading techniques, you create realistic or stylized visual effects tailored to specific rendering needs.
Choosing Appropriate Materials
Materials ensure realistic light interaction based on reflectivity, roughness, and transparency properties. Your selection depends on the context:
- Game assets prioritize performance with optimized shaders.
- Archaeological reconstructions demand historical accuracy.
- 3D printing requires attention to material thickness and structural integrity.
- Geological models use layered materials with controlled transparency.
Creating Custom Shaders
Custom shaders allow you to control light interaction through surface properties, light behavior, and texture manipulation. By using shader languages like HLSL or node-based editors, you can create tailored visual effects that balance quality with performance.
Applying Textures and Materials Effectively
You should apply materials systematically using base textures, detail maps, bump/displacement, specular, and normal maps. Optimization strategies include using appropriate resolutions, material instances, texture atlasing, and adhering to PBR principles.
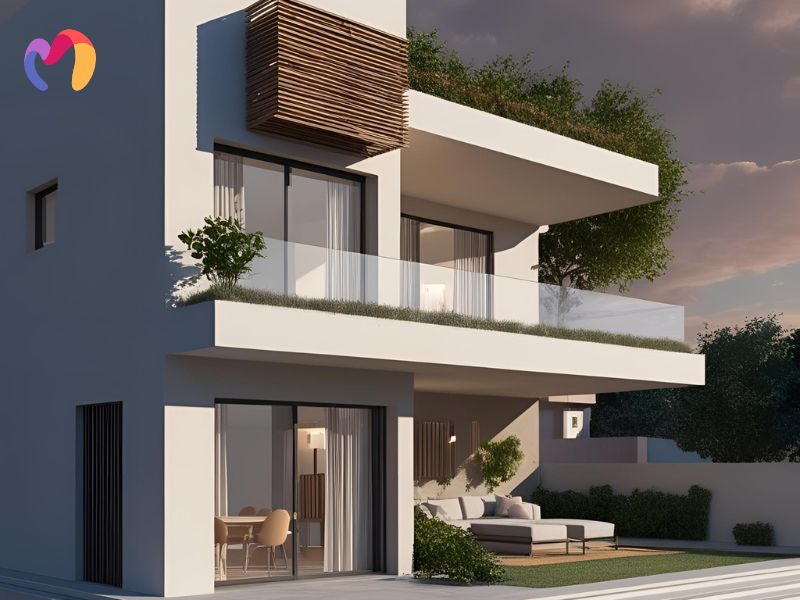
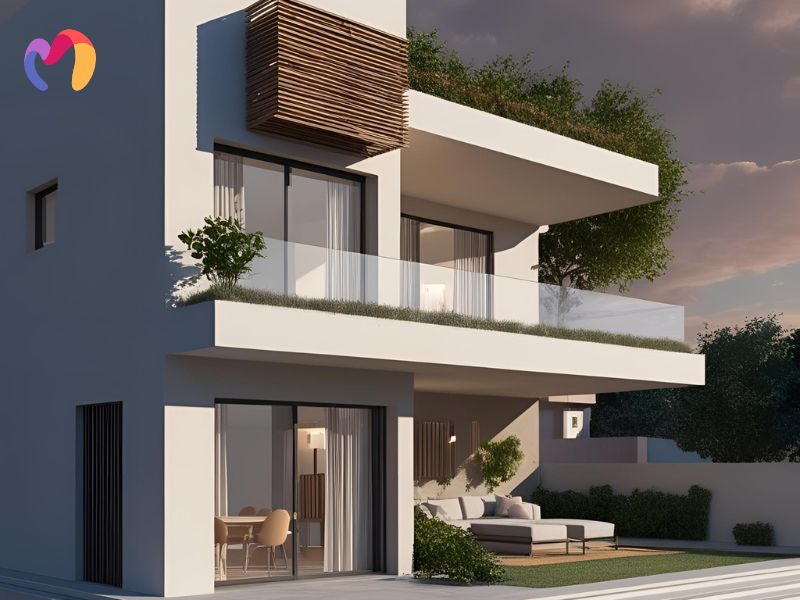
Step 6. Lighting and Rendering
Lighting, rendering, and post-processing shape how 3D models appear, defining realism and visual impact. Proper lighting builds depth, rendering transforms raw geometry into refined images, and post-processing enhances final compositions.
Setting Up Lighting for 3D Scenes
To establish a strong lighting foundation, you should implement the three-point lighting system:
- Key Light: Main source placed at an angle for strong highlights
- Fill Light: Softer light reducing deep shadows
- Back Light: Separates subjects from backgrounds, adding depth
Our scenes utilize various light types (directional, point, spot, area) with fine-tuned intensity, color temperature, shadows, bounce, and falloff settings.
Rendering Techniques and Best Practices
Rendering converts 3D data to images using engines like V-Ray, Arnold, and Corona with techniques including global illumination, ambient occlusion, and physically based rendering.
Optimization strategies include:
- Adjusting sampling rates to balance noise reduction with render time
- Selecting appropriate resolution and output formats for intended use
- Utilizing render layers for isolated element control
- Implementing proxy objects to manage high-poly assets efficiently
Post-Processing and Compositing
Post-processing refines renders through adjustments and layering techniques. Color grading, contrast adjustments, and atmospheric effects enhance depth and realism. Some common techniques include:
- Depth of Field: Blurs background for cinematic focus.
- Render Passes: Separates elements like reflections, shadows, and specularity for precise control.
- Compositing Effects: Adds lens flares, fog, or haze to heighten immersion.
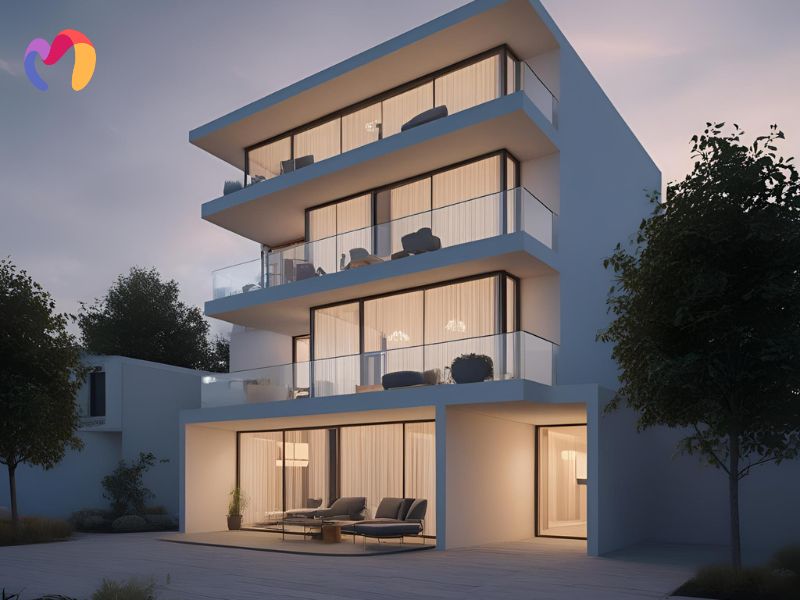
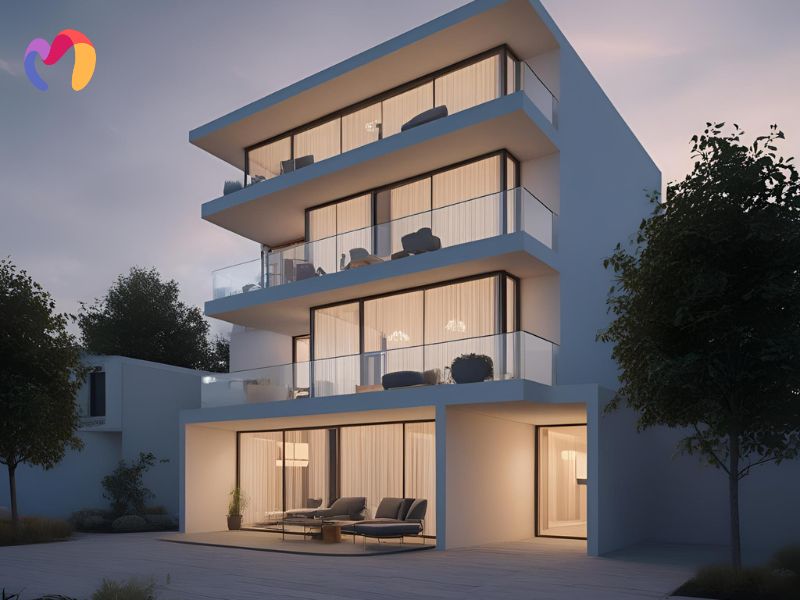
Step 7. Refinement and Quality Assurance
A well-structured quality assurance process is essential for delivering reliable, high-performance 3D models. Through meticulous testing and optimization, you ensure that every model meets industry standards and functions seamlessly across its intended platforms.
- Reviewing and Testing 3D Models: You evaluate geometry, topology, and UV mapping by analyzing polygon count, edges, and unwrapping. Additionally, you test animation, rendering properties, and real-time performance using specialized software.
- Optimizing Performance and Efficiency: Optimization includes reducing polygon density in non-essential areas, efficient UV mapping, mesh simplification, texture atlasing, LOD implementation, and material consolidation. These techniques ensure smooth performance across different platforms while maintaining visual integrity.
- Fixing Common Issues and Errors: By conducting mesh analysis, welding vertices, adjusting face orientation, and performing retopology, you resolve non-manifold geometry and topology issues. Implementing systematic validation procedures helps prevent recurring problems, reducing correction time and ensuring your models are production-ready.
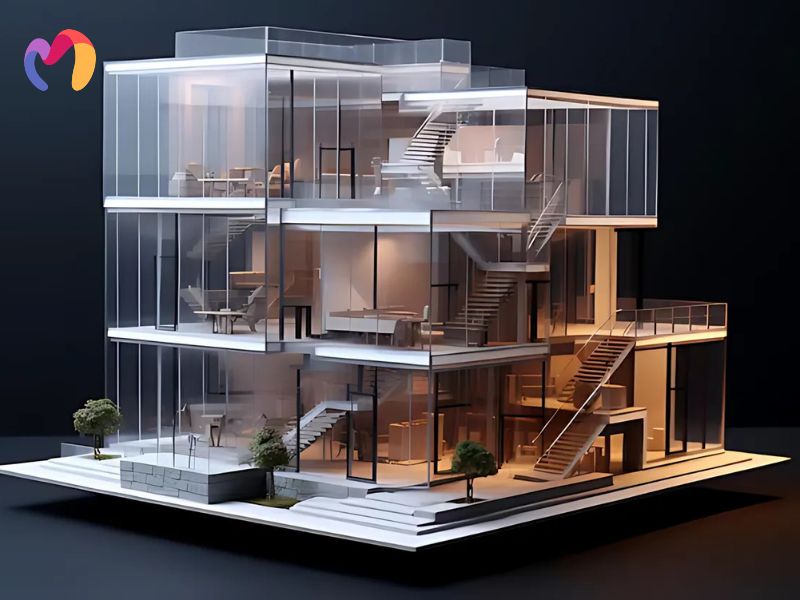
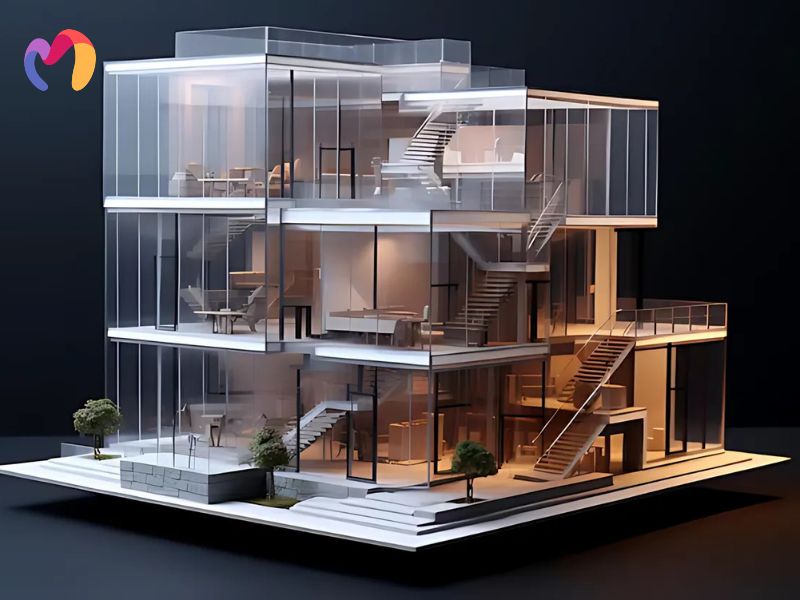
Step 8. Final Delivery and Project Completion
Delivering a project is more than just handing over files, it’s about ensuring assets are well-organized, properly documented, and fully optimized for seamless client integration.
- Preparing Files for Client Delivery
Final delivery requires structured file preparation and precise formatting. You need to ensure all 3D assets are accessible and ready for use by following standardized conventions. Deliverables are provided in multiple formats based on project needs:
- Native source files: (.max, .mb, .blend)
- Exchange formats: (.fbx, .obj, .dae)
- Rendered outputs: (.jpg, .png, .tiff)
- Project documentation: (.pdf)
Before delivery, you must conduct quality checks by ensuring mesh integrity, checking map material and texture assignments, verifying correct scale and units, checking animation playback if applicable, organizing the folder structure properly, and ensuring all necessary assets are available.
- Creating Documentation and Guidelines
Clear documentation ensures a smooth transition from model creation to client implementation. It includes structured technical details, project breakdowns, and usage instructions.
- Documentation covers:
- Model hierarchy and organization
- Material and texture specifications
- Rendering settings and format requirements
- Technical constraints and optimization strategies
- Implementation steps
- Troubleshooting and maintenance guidelines
- Handling Revisions and Feedback
You should manage revisions by logging modifications, using structured feedback forms, maintaining open communication, and storing versions methodically for tracking changes and potential rollbacks.
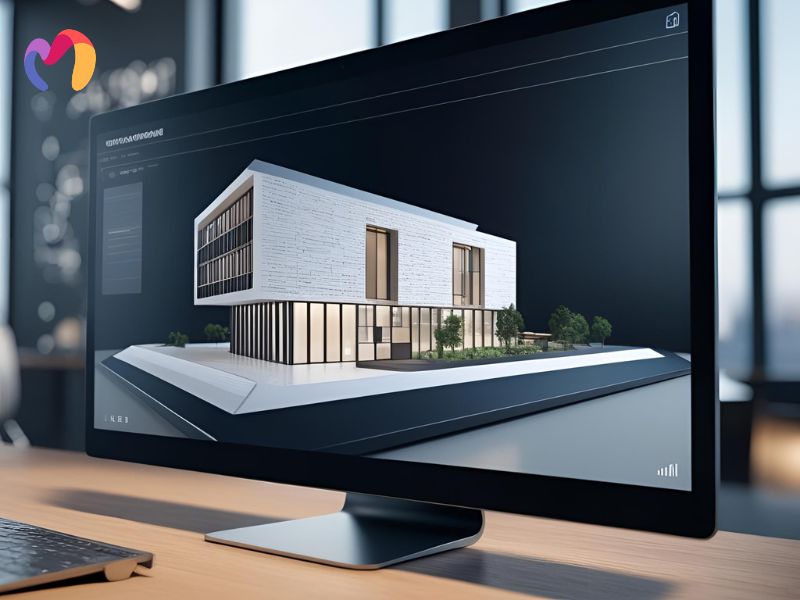
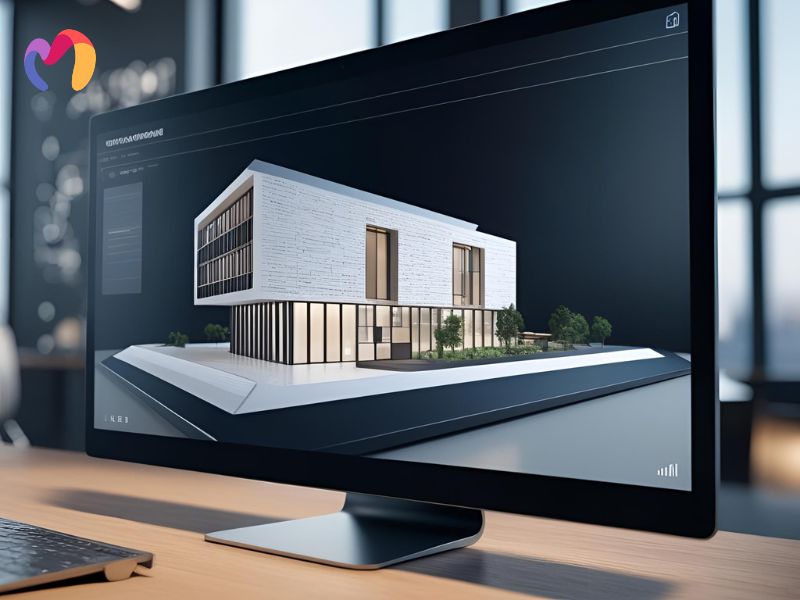
Conclusion
The 3D modeling workflow consists of eight crucial steps that ensure the production of high-quality models, from planning to delivery. This structured methodology allows for efficient project management and strict quality control to meet industry standards and client needs.
For more insights, visit 3DMAXTER for related blog posts or explore our extensive collection of 3D models.
3DMAXTER LTD
- Email: [email protected]
- Phone: +1 (929) 450-2898
- Address: 95-38 Queens Blvd, Rego Park, NY 11374, USA